Specific Process Knowledge/Etch/DRIE-Pegasus/Pegasus-2/ORE with Al2O3 mask: Difference between revisions
Line 19: | Line 19: | ||
Using patterned samples of 1 μm pillars with 50 nm of Al<sub>2</sub>O<sub>3</sub>. After the tests, approximately 32nm of Al<sub>2</sub>O<sub>3</sub> were still intact. | Using patterned samples of 1 μm pillars with 50 nm of Al<sub>2</sub>O<sub>3</sub>. After the tests, approximately 32nm of Al<sub>2</sub>O<sub>3</sub> were still intact. | ||
<br clear="all" /> | <br clear="all" /> | ||
[[File:compare pillars.png| | [[File:compare pillars.png|400px|left|thumb|'''''Pillars with different etching times.''''']] | ||
{| border="1" style="text-align: center; width: 650px; height: 200px" | {| border="1" style="text-align: center; width: 650px; height: 200px" | ||
|+ 1μm Pillar recipe from March 2022 - #244 = 122 min | |+ 1μm Pillar recipe from March 2022 - #244 = 122 min | ||
Line 39: | Line 39: | ||
=== Holes === | === Holes === | ||
Using patterned samples of 1 μm holes with 50 nm of Al<sub>2</sub>O<sub>3</sub>. After the tests, approximately 28nm of Al<sub>2</sub>O<sub>3</sub> were still intact. | Using patterned samples of 1 μm holes with 50 nm of Al<sub>2</sub>O<sub>3</sub>. After the tests, approximately 28nm of Al<sub>2</sub>O<sub>3</sub> were still intact. | ||
[[File:holes 17 e 10 um.png| | [[File:holes 17 e 10 um.png|400px|left|thumb|'''''Holes profile.''''']] | ||
{| border="1" style="text-align: center; width: 900px; height: 200px" | {| border="1" style="text-align: center; width: 900px; height: 200px" | ||
|+ 1μm holes recipe from March 2022 | |+ 1μm holes recipe from March 2022 |
Revision as of 11:21, 19 January 2023
Feedback to this page: click here
THIS PAGE IS UNDER CONSTRUCTION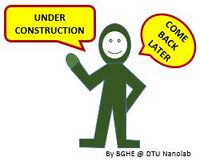
By Maria Farinha @nanolab, Jan 2023
Important! The pressure settings used below may no longer be permitted, always check with the Dry etch group.
As stated by Nguyen et al., the SF6 and O2 fluxes are only separated after 4 s during the C-step. Shorter time steps than that do not execute the function of the clearing. After testing recipes with only 2 s of clearing and with no clear step, it was understood it could be eliminated, showing more depth as well as less undercut when going for shorter cycles. From then on, not CORE but ORE recipes were applied D/E = O/RE.
Moreover, during the E-step, the MFC (mass flow controller) presented a delay to read the pressure when compared with the power, creating unwanted bias. To fight it, the E-step was divided into E1 and E2. The E1 of only 2 s is enough to stabilize the pressure, and E2 the profile is etch correctly, without the unwanted bias.
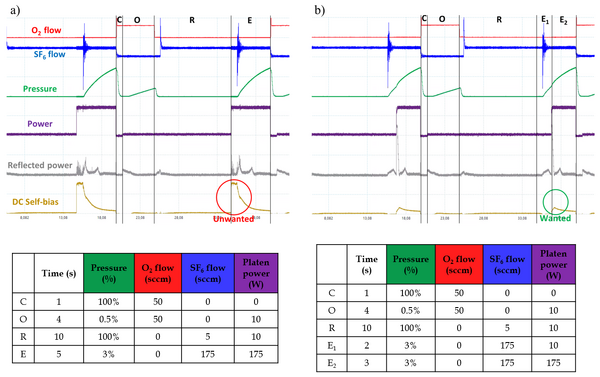
Pillars
Using patterned samples of 1 μm pillars with 50 nm of Al2O3. After the tests, approximately 32nm of Al2O3 were still intact.
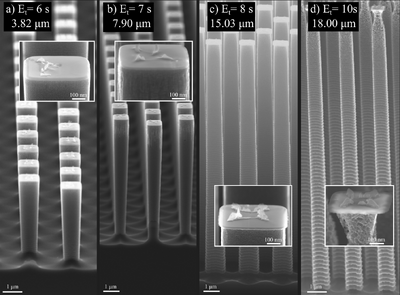
Time (s) | Pressure (valve control) | O2 flow (SCCM) | SF6 flow (SCCM) | Platen power (W) | |
---|---|---|---|---|---|
O-step | 10 | 3% | 200 | 0 | 40 |
R-step | 10 | 100% | 0 | 5 | 40 |
E1-step | 2 | 4% | 0 | 350 | 40 |
E2-step | 7 | 4% | 0 | 350 | 300 |
* Pillars profile effect when varying the etch time.
Holes
Using patterned samples of 1 μm holes with 50 nm of Al2O3. After the tests, approximately 28nm of Al2O3 were still intact.

Time (s) | Pressure | O2 flow (SCCM) | SF6 flow (SCCM) | Platen power (W) | Coil power (W) | |
---|---|---|---|---|---|---|
O-step | 10 | 220 mTorr | 200 | 0 | 40 | 0 |
R-step | 10 | 100% | 0 | 40 | 40 | 0 |
E1-step | 2 | 220 mTorr | 0 | 1200 | 0 | 0 |
E2-step | 1-5 | 220 mTorr | 0 | 1200 | 1 | 2000 |
* For #288 cycles, 120 min, the profile depth reaches 17.6 μm. For #144 cycles, 60 min, the profile depth reaches 10.1 μm. Width variation presented in the pictures.
Nanoholes
Time (s) | Pressure (valve control) | O2 flow (SCCM) | SF6 flow (SCCM) | Platen power (W) | |
---|---|---|---|---|---|
O-step | |||||
R-step | |||||
E1-step | |||||
E2-step |