Specific Process Knowledge/Lithography/Aligners/Aligner: Maskless 02 processing: Difference between revisions
Line 23: | Line 23: | ||
[[Image:AZ spectral sensitivity.gif|400x400px|thumb|Spectral sensitivity of AZ resists represented as optical absorption. From https://www.lithoprotect.com/]] | [[Image:AZ spectral sensitivity.gif|400x400px|thumb|Spectral sensitivity of AZ resists represented as optical absorption. From https://www.lithoprotect.com/]] | ||
Dose compared to 365nm exposure (using e.g. Aligner: MA6-2 or Aligner: Maskless 01): | |||
{|border="1" cellspacing="1" cellpadding="7" style="text-align:center;" | |||
|- | |||
|- | |||
|-style="background:silver; color:black" | |||
| | |||
!375nm | |||
!405nm | |||
|- | |||
|- | |||
|-style="background:WhiteSmoke; color:black" | |||
!AZ 5214E | |||
|1 | |||
|1.15 <sup>1)</sup> | |||
|- | |||
|- | |||
|-style="background:LightGrey; color:black" | |||
!AZ 4562 | |||
|1 | |||
|1.15 <sup>1)</sup> | |||
|- | |||
|- | |||
|-style="background:WhiteSmoke; color:black" | |||
!AZ MiR 701 | |||
|1 | |||
|1.15 <sup>1)</sup> | |||
|- | |||
|- | |||
|-style="background:LightGrey; color:black" | |||
!AZ nLOF 2020 | |||
|1 | |||
|1.15 <sup>1)</sup> | |||
|- | |||
|- | |||
|-style="background:WhiteSmoke; color:black" | |||
!SU-8 | |||
|1 | |||
|1.15 <sup>1)</sup> | |||
|- | |||
|} | |||
<br clear="all" /> | <br clear="all" /> |
Revision as of 21:29, 27 March 2019
Feedback to this page: click here
THIS PAGE IS UNDER CONSTRUCTION
Exposure technology
Aligner: Maskless 02 is not a direct writer. In the maskless aligner, the exposure light is passed through a spatial light modulator, much like in a video projector, and projected onto the substrate, thus exposing an area of the design at a time. The substrate is exposed by scanning the exposure field across the substrate in a succession of stripes.
The light source is a laser diode (array) with a wavelength of 375nm (2.8W) or 405nm (8W). The spacial light modulator is a digital micro-mirror device. The individual mirrors of the DMD are switched in order to represent the design, and the laser is flashed in order to yield the desired exposure dose. This image is projected onto the substrate through a lens(system). The projected image yields a pixel size of 160nm X 160nm at wafer scale. The image is scanned across the substrate, in order to expose the entire design, each stripe overlapping (2 or 4 times) in order to minimize uniformity effects and stitching errors.
The writing head of the Aligner: Maskless 02 moves only in the z-direction. Using an optical (or pneumatic) focusing system, the maskless aligner is able to do real-time autofocus. The defocus process parameter is used to compensate offsets in the focusing mechanism, and to optimize printing quality in different resists and varying thicknesses. The stage of the Aligner: Maskless 02 moves only in x and y. It has no theta-axis. All rotation during alignment is thus accomplished by transformation of the input design.
Process Parameters
Exposure dose
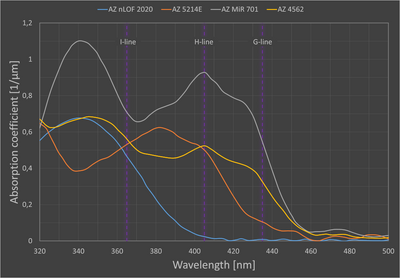
Dose compared to 365nm exposure (using e.g. Aligner: MA6-2 or Aligner: Maskless 01):
375nm | 405nm | |
---|---|---|
AZ 5214E | 1 | 1.15 1) |
AZ 4562 | 1 | 1.15 1) |
AZ MiR 701 | 1 | 1.15 1) |
AZ nLOF 2020 | 1 | 1.15 1) |
SU-8 | 1 | 1.15 1) |
Defocus
Exposure mode
(high quality, fast)
Resolution
- 5206E 0.5µm 375nm, dev 2xSP30s
Fast: 60mJ/cm2; defoc -6 (1µm, not optimized)
Quality: 60mJ/cm2; defoc -6 (~750nm, not optimized)
- 5214E 1.5µm 405nm, dev SP60s
Fast: 90mJ/cm2; defoc -2 (1-2µm)
- 5214E 1.5µm 375nm, dev SP60s
Fast: 65mJ/cm2; defoc 2 (~1µm)
Quality: 65mJ/cm2; defoc 2 (~750nm)
- MiR 701 1.5µm 405nm, PEB 60s@110°C dev SP60s
Fast: 200mJ/cm2; defoc -5 (~1µm, not optimized)
- MiR 701 1.5µm 375nm, PEB 60s@110°C dev SP60s
Fast: 170mJ/cm2; defoc -5 (1µm)
Quality: 180mJ/cm2; defoc -6 (750nm)
- nLOF 2020 2µm 375nm, PEB 60s@110°C dev SP60s
Fast: 400mJ/cm2; defoc 5 (~1µm, not optimized)
Quality: 400mJ/cm2; defoc 0 (1µm)
Writing speed
(high quality, fast)
- Speed vs. area (375nm)
- Online
- Offline
- Speed vs. dose (375nm + 405nm)
Features
Substrate centring and flat alignment
During substrate detection, the sample is scanned along the X- and Y-axes, as well as diagonally. From these measurements, the size (diameter) of the substrate is calculated, as well as the stage position matching the center of the substrate. This stage position will be the default origin for the subsequent exposure.
At the end of substrate detection, the sample is scanned twice along the bottom edge (flat), in order to determine the substrate rotation. This angle will be presented in the exposure panel along with the option to expose the design rotated in order to compensate for this angle, i.e. aligned to the flat/edge of the substrate.
- Substrate centering + flat alignment test
Labelling
HIMT\Designs\Labels\labelfile.lbl (tab-delimited ASCII file with special header).
X | Y | UNIT | HEIGHT | UNIT | TITLE
-16000 | -46000 | um | 2000 | um | TARAN DTU Nanolab 20190320
This produces a 2mm high, approximately 32mm long wafer ID at the flat of a 4" wafer.
Some special characters are not allowed (e.g. ';').
High Aspect Ratio mode
- Intensity vs. aperture (405nm + 375nm)
- Dose test for 1.5µm MiR (405nm + 375nm)
Alignment
Top Side Alignment
- 4 marks (before final installation)
- Scaling (375nm, high res camera)
Back Side Alignment
- Tested, 2-3µm error in X observed
- Corrected
Advanced Field alignment (TSA)
- 4 marks, 25 fields (375nm, high res camera)
- Scaled first print, 10 fields (375nm, high res camera)
- 4 marks, 25 fields (405nm, high res camera)