Specific Process Knowledge/Thin film deposition/Temescal: Difference between revisions
No edit summary |
|||
Line 1: | Line 1: | ||
'''Feedback to this page''': '''[mailto:labadviser@danchip.dtu.dk?Subject=Feed%20back%20from%20page%20http://labadviser.danchip.dtu.dk/. | '''Feedback to this page''': '''[mailto:labadviser@danchip.dtu.dk?Subject=Feed%20back%20from%20page%20http://labadviser.danchip.dtu.dk/index.php?title=Specific_Process_Knowledge/Thin_film_deposition/Temescal click here]''' | ||
<!-- Replace "http://labadviser.danchip.dtu.dk/..." wih the link to the Labadviser page--> | <!-- Replace "http://labadviser.danchip.dtu.dk/..." wih the link to the Labadviser page--> | ||
Revision as of 13:41, 17 September 2018
Feedback to this page: click here
E-Beam Evaporator (Temescal)
The Temescal is a system for depositing metals by electron-beam evaporation. In e-beam evaporation, the deposition is line-of-sight directed from the source, which means it will coat only the surface of the sample facing directly towards the source. This makes it very useful for example for metals for lift-off. The system also has an ion source for in-situ Argon sputtering that can be used either for cleaning samples prior to deposition or to modify the film during deposition.
Wafers are loaded into the top of the chamber, which acts as a loadlock as it can be separated from the rest of the chamber by a large gate valve. Deposition will happen on all samples that are loaded together. You can load up to four 6" wafers or three 8" wafers for deposition on surfaces facing the evaporation source, or on up to one 6" wafer for tilted deposition (smaller samples may be tilted more). By using sample holder inserts, you can deposit metals on samples of different sizes and shapes. Only one metal can be deposited at a time, but you can deposit many layers of different metals one after the other. The system contains 6 metals at a time and the metals are exchanged based on user requests, so please request the metals you wish well in advance.
The user manual, user APV, and contact information can be found in LabManager:
E Beam Evaporator (Temescal) in LabManager
Process information
Materials for e-beam evaporation
- Aluminium (Al)
- Chromium (Cr)
- Copper (Cu)
- Gold (Au)
- Molybdenum (Mo)
- Nickel (Ni)
- Palladium (Pd)
- Platinum (Pt)
- Silver (Ag)
- Tantalum (Ta)
- Tin (Sn)
- Titanium (Ti)
- Tungsten (W) - thinner layers
Note that to date (July 2018) we have processes available for deposition of Al, Cr, Au, Ni, Pd, Ag, Ti, and W as well as Ru. More will be available as they are requested, e.g., Nb is expected in the early fall of 2018.
Purpose | Deposition of metals |
|
---|---|---|
Performance | Film thickness |
|
Deposition rate |
| |
Thickness uniformity |
| |
Thickness accuracy |
| |
Process parameter range | Process Temperature |
|
Process pressure |
| |
Source-substrate distance |
| |
Substrates | Batch size |
|
Substrate material allowed |
| |
Material allowed on the substrate |
|
* For thicknesses above 600 nm please request permission so we can ensure that enough material will be present.
** Defined as the ratio of the standard deviation to the average of the measurement made using the DektakXT. For further details see the acceptance test.
Quality control (QC) for the Temescal
We are still developing the QC procedure for the Temescal (September 2018).
The e-beam and the Cu hearth
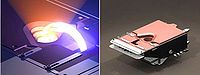
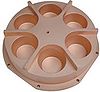
At the start of the deposition and for every 100 nm, please check that the e-beam hits the target material that you would like to evaporate rather than the heath next to the pocket or the bottom of the pocket. I.e., check that the e-beam sweep has not shifted, which could happen if the filament assembly has been distorted by heat for example, and also check that there is enough material in the pocket, so that you do not burn a hole in the bottom of the pocket. If you burn a hole in the bottom of the pocket, cooling water may leak into the chamber and it may flood!
Thickness measurement
The machine measures the thickness of the growing film with a Quartz Crystal Microbalance or QCM. The machine calls it the Xtal (crystal). This is a very thin piece of quartz that resonates at about 5-6 MHz when a voltage is applied across it. The resonance frequency varies with the mass of the crystal, and when material is deposited on one side of it, the frequency changes. This is measured by the crystal monitor, which can then calculate the deposited thickness.
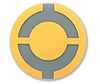
The thickness calculation depends on the material density as well as other physical factors. A so-called tooling factor is used to adjust the calculation based on the geometry of the setup, since the crystal is not in the same place as the wafer holders and the actual thickness deposited on the crystal is lower than on the samples.
The tooling factor is calibrated for a particular deposition rate. It may not be perfectly accurate for other deposition rates, but should easily be within the 10 % accuracy that we test for in our quality control measurements. For very thin films the thickness measurement will be less accurate than for thicker films.
The machine gives a rough number for the crystal lifetime simply based on how thick a layer it calculates has been deposited on it. If many layers have been deposited and there is stress in the layers (e.g., in Cr, Ni, or Ru layers), there may be partial delamination, which can make the thickness measurement inaccurate. In this case the lifetime estimate given by the machine will be inaccurate. If you think the crystal is not measuring correctly, please let us know. We exchange the crystals usually around 20 % lifetime use.
Heating during deposition
If the material you are depositing requires a lot of heat to evaporate, the substrates may get warm during the deposition.
A temperature test of a 100 nm Al deposition at 10 Å/s showed that the back of the wafer stays below 37 oC. The same is true for 10 nm Ti/90 nm Au at 10 Å/s. In contrast deposition of 60 nm W at about 1 Å/s heated the substrate to above 120 oC.
Al requires intermediate power (about 450 mA and 1000 V supplied to the filament that creates the e-beam) while W requires high power (about 600 mA at 1000 V supplied to the filament).
Please ask us if you need to test the heating of the substrates before making a deposition with the metal you need (contact thinfilm@danchip.dtu.dk).