Specific Process Knowledge/Thin film deposition/Deposition of Gold/Adhesion layers: Difference between revisions
Line 17: | Line 17: | ||
From the cross section profile of the 2nm Au sample (Fig. 2a), it is clear that Au, when deposited directly on SiO2, in order to reduce the interface energy, forms a nanoparticle-like layer in contrast to a continuous film. The diameter of the nanoparticles is about 10 nm. The nanoparticle morphology is confirmed by AFM analysis (Fig. 2b). The RMS surface roughness was measured to be 2.4 nm. For comparison, the RMS roughness of the SiO2 substrate was 0.3 nm. When the thin-film nominal thickness is increased to 20 nm (20nm Au sample, Fig. 2c), the Au layer becomes continuous, but a certain degree of surface roughness is still present due to grain coalescence. The AFM image (Fig. 2d) shows an RMS surface roughness of 1.0 nm, which is significantly lower than the 2nm Au sample. | From the cross section profile of the 2nm Au sample (Fig. 2a), it is clear that Au, when deposited directly on SiO2, in order to reduce the interface energy, forms a nanoparticle-like layer in contrast to a continuous film. The diameter of the nanoparticles is about 10 nm. The nanoparticle morphology is confirmed by AFM analysis (Fig. 2b). The RMS surface roughness was measured to be 2.4 nm. For comparison, the RMS roughness of the SiO2 substrate was 0.3 nm. When the thin-film nominal thickness is increased to 20 nm (20nm Au sample, Fig. 2c), the Au layer becomes continuous, but a certain degree of surface roughness is still present due to grain coalescence. The AFM image (Fig. 2d) shows an RMS surface roughness of 1.0 nm, which is significantly lower than the 2nm Au sample. | ||
[[File:Picture1.png|350px|center|thumb|Fig. 2: TEM cross section images and 300x300 nm AFM images of the 2nm Au sample (a-b) and of the 20nm Au sample (c-d).]] | |||
From the TEM bright field cross section analysis of the 2nm Ti/2nm Au sample, it is observed that 2 nm of Ti forms a continuous layer below the Au layer (Fig. 3a). The Au layer is continuous over the Ti, indicating that Ti is responsible for an interface energy decrease, acting as an adhesive. The AFM analysis of the same sample confirmed the continuous structure, and an RMS surface roughness of 0.8 nm was measured (Fig. 3b). The 2nm Ti/20nm Au sample also shows a smoother film compared to the 20nm Au sample (Fig. 3c), and the AFM analysis shows an RMS surface roughness of 0.5 nm (Fig. 3d), very similar to the one of the Si substrate. | From the TEM bright field cross section analysis of the 2nm Ti/2nm Au sample, it is observed that 2 nm of Ti forms a continuous layer below the Au layer (Fig. 3a). The Au layer is continuous over the Ti, indicating that Ti is responsible for an interface energy decrease, acting as an adhesive. The AFM analysis of the same sample confirmed the continuous structure, and an RMS surface roughness of 0.8 nm was measured (Fig. 3b). The 2nm Ti/20nm Au sample also shows a smoother film compared to the 20nm Au sample (Fig. 3c), and the AFM analysis shows an RMS surface roughness of 0.5 nm (Fig. 3d), very similar to the one of the Si substrate. | ||
<gallery widths=" | <gallery widths="350px" heights="350px" perrow="2" halign="center"> image:Picture5.png|Fig. 3: TEM cross section images and 300x300 nm AFM images of the 2nm Ti/2nm Au sample (a-b) and of the 2nm Ti/20nm Au sample (c-d). | ||
image:Picture5.png|Fig. 3: TEM cross section images and 300x300 nm AFM images of the 2nm Ti/2nm Au sample (a-b) and of the 2nm Ti/20nm Au sample (c-d). | |||
image:Picture7.png|Fig. 4: TEM cross section images and 300x300 nm AFM images of the 2nm Cr/2nm Au sample (a-b) and of the 2nm Cr/20nm Au sample (c-d). </gallery> | image:Picture7.png|Fig. 4: TEM cross section images and 300x300 nm AFM images of the 2nm Cr/2nm Au sample (a-b) and of the 2nm Cr/20nm Au sample (c-d). </gallery> | ||
Revision as of 11:56, 14 August 2018
Adhesion layers
The deposition of metal thin-film structures on dielectric or semiconductor substrates is important in a wide range of micro/nanofabrication applications (plasmonics, metamaterials, organic transistors, substrates for graphene growth, field effect devices).
Noble metals such as Au, Ag, and Pt are often used for the fabrication of these structures. Noble metals are preferred for their high thermal and electrical conductivities, strong and unique optical resonances in the visible and near-infrared (NIR) region of the electromagnetic spectrum due to the resonant response of their free electrons to the electric field of light, and chemical inertness. However, their chemical inertness is also a problem during the fabrication process, because the layers adhere poorly to the substrate, leading to different phenomena like delamination, peeling and deterioration of device performance over time.
An empiric approach has been applied to the adhesion enhancement, leading to the application of extremely thin adhesion layers between the substrate and the noble metal films. The most used of these adhesion layers are transition metals like Ti and Cr, but the advantages of using these materials as adhesion layers are poorly understood.
Fig. 1 represents the simplified adhesion layer model usually used in the micro and nanofabrication community for a generic bilayer system. In this model, the adhesion layer and the noble metal over-layer are deposited sequentially by PVD and are considered to be completely uniform and in perfect contact. Ti and Cr are known to be more chemically reactive than noble metals and thereby increase the adhesion as they chemically bind to the substrate. However, the model does not include any layer-layer interaction. Moreover, it is considered to be independent of the thin-film thickness. Due to the continuous miniaturization of structures and devices, the total metal thin-film thicknesses have reached tens of nanometers, with the thickness of the over-layer approaching the one of the adhesion layer. In these conditions it is unclear if the simplified model is still adequate.
Here the characterization work carried out on two main thin-film systems, Cr/Au and Ti/Au stacks, is presented.
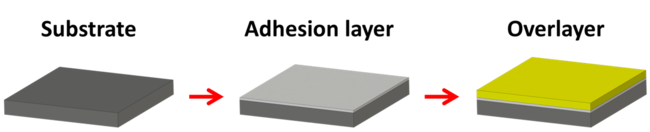
Adhesion layer effect on Au thin films
Effect on Au film morphology, grain size and texture
From the cross section profile of the 2nm Au sample (Fig. 2a), it is clear that Au, when deposited directly on SiO2, in order to reduce the interface energy, forms a nanoparticle-like layer in contrast to a continuous film. The diameter of the nanoparticles is about 10 nm. The nanoparticle morphology is confirmed by AFM analysis (Fig. 2b). The RMS surface roughness was measured to be 2.4 nm. For comparison, the RMS roughness of the SiO2 substrate was 0.3 nm. When the thin-film nominal thickness is increased to 20 nm (20nm Au sample, Fig. 2c), the Au layer becomes continuous, but a certain degree of surface roughness is still present due to grain coalescence. The AFM image (Fig. 2d) shows an RMS surface roughness of 1.0 nm, which is significantly lower than the 2nm Au sample.

From the TEM bright field cross section analysis of the 2nm Ti/2nm Au sample, it is observed that 2 nm of Ti forms a continuous layer below the Au layer (Fig. 3a). The Au layer is continuous over the Ti, indicating that Ti is responsible for an interface energy decrease, acting as an adhesive. The AFM analysis of the same sample confirmed the continuous structure, and an RMS surface roughness of 0.8 nm was measured (Fig. 3b). The 2nm Ti/20nm Au sample also shows a smoother film compared to the 20nm Au sample (Fig. 3c), and the AFM analysis shows an RMS surface roughness of 0.5 nm (Fig. 3d), very similar to the one of the Si substrate.
-
Fig. 3: TEM cross section images and 300x300 nm AFM images of the 2nm Ti/2nm Au sample (a-b) and of the 2nm Ti/20nm Au sample (c-d).
-
Fig. 4: TEM cross section images and 300x300 nm AFM images of the 2nm Cr/2nm Au sample (a-b) and of the 2nm Cr/20nm Au sample (c-d).
In contrast to the case with the Ti adhesion layer, TEM bright field analysis of the 2nm Cr/2nm Au sample shows a single continuous layer (Fig. 4a). The AFM RMS surface roughness is 1.2 nm (Fig. 4b). Increasing the nominal Au thickness to 20 nm for the 2nm Cr/20nm Au sample, the film still presented a single-layer morphology (Fig. 4c), while the RMS surface roughness decreased to 0.6 nm (Fig. 4d).
To investigate the crystal orientation of the metal thin-�lms, tramsimission Kikuchi diffraction was used (Fig. 5a). The nanostructure of the 20nm Au �lm has a bimodal grain size distribution (Fig. 5b). While the smaller grains have di�erent crystal orientations, the large grains (blue color) all have [111] orientation. Microstructural evolution and growth of metal thin-�lms deposited by physical vapor deposition on amorphous dielectric substrates follows island growth. The �rst thin-�lm growth step is the nucleation of small islands once the activation barrier and the critical nuclei size have been overcome. It is followed by a second step of island growth, during which the impinging atoms contribute to increase island size. The third step, usually happening simultaneously with step 2, is island coalescence, where a strong driving force is present for coarsening through surface atom di�usion and grain boundaries (GB) motion. During this process, the island growth is driven by the minimization of surface and interface energy. Fig. 5.4a represents two Au islands having di�erent crystal orientations. In particular they have the (111)- and (100)-facets, respectively, parallel to the substrate surface. The growth of these islands is dependent on their orientation (Fig. 5.4b): for Au, which has a face-centered cubic unit cell, the (100) surface has a higher surface energy than the (111) surface, and to minimize energy, the (100) surface grows faster. Islands having (100) or (110) facets parallel to the substrate grow faster in the vertical direction, while islands with (111) facets parallel to the substrate grow faster laterally. The result
is a continuous �lm, having laterally larger and atter islands with [111] crystal direction, and laterally smaller but taller islands with [100] and [110] orientations [106].
The samples with 20 nm Au layer were analyzed with TKD. The addition of the adhesion layer had in both cases a profound impact on grain size and orientation of the Au �lm, as visible in Fig. 5.7a and 5.7c. The image shows
small grains mainly oriented in the [111] crystal direction, with an average grain size of 40 nm for Ti (Fig. 5.7b) and 36 nm for Cr (Fig. 5.7d). During the collection of the TKD maps, only the Kikuchi patterns produced by the electron scattering from the Au layer were recorded and indexed. Cr and Ti layers did not contribute to the pattern formation due to two main reasons: i) they are too thin to produce enough scattered electrons and ii) they are worse electron scattering centers tahn Au because they have a lower atomic number.
The smaller grain size is attributed to an enhanced wetting of the deposited Au promoted by the adhesion layer. The enhanced wetting behaviour increases the number of nucleation sites compared to the pure Au �lm case, where Au is evaporated directly onto the SiO2 surface. This eventually leads to a much denser nucleation of the Au grains, which at the same time facilitates the inter-di�usion of Au atoms. The enhanced wetting might be due to the formation of Ti-Au and Cr-Au bonds
The very dominant [111] crystal orientation observed implies a decrease of the energy barrier for the formation of the energetically most favourable Au crystal structure. This is promoted by the denser nucleation and stronger inter-di�usion of Au atoms described above. In contrast to the pure Au case, all the grains have the same di�usion rate of the (111) exposed planes, and therefore the grains grow with a narrow grain size distribution. Since the �lm has been deposited at room temperature, the system did not have enough energy to overcome the energy barrier for grain coalescence, hence resulting in grains with a small average size. For the Cr case, also small grains with [100] and [110] crystal orientations were detected. This might suggest that for Au on Cr the [111] orientation is energetically less favored with respect to the [100] and [110] orientations compared to the Ti/Au case.
Bilayer chemical composition and elemental distribution
Adhesion layer effect on bilayer thin-film electrical resistivity
Adhesion layer model
Recommendations for nanodevice fabrication
Nano-optic devices
Nano-electronic devices
Adhesion layer impact on Au �film stability with temperature
allic bond with gold. 5 nm to 10 nm thick of Cr or Ti is commonly used and it is important to deposit Cr or Ti and then immediately Au. If the vacuum chamber is opened in between, the surface of Cr or Ti will get oxidized and that will give a poor adhesion. If a gold layer needs to be deposited directly on Silicon, then native oxide has to be removed by deep in diluted HF and immediately load the evaporation chamber. And after the deposition, the wafer has to be heated op to get some Au-Si diffusion which improves the adhesion.