Specific Process Knowledge/Back-end processing/Polymer Injection Molder/Injection: Difference between revisions
Line 1: | Line 1: | ||
== | == Injection == | ||
Injection parameters are very important in injection molding optimization. The injection speed will of course determine how long time it takes to fill the cavity. It also has a large influence on the rheology of the polymer melt. Generally, viscosity of polymer melt will decrease with increasing injection speed (an effect known as shear thinning). The injection speed also influences how structures are filled and to what extent the air inside the cavity has time to escape as polymer is injected. It therefore often takes some optimization to achieve all desired sample properties. Injection speed settings are adjusted in the ''''Inject'''' screen: | Injection parameters are very important in injection molding optimization. The injection speed will of course determine how long time it takes to fill the cavity. It also has a large influence on the rheology of the polymer melt. Generally, viscosity of polymer melt will decrease with increasing injection speed (an effect known as shear thinning). The injection speed also influences how structures are filled and to what extent the air inside the cavity has time to escape as polymer is injected. It therefore often takes some optimization to achieve all desired sample properties. Injection speed settings are adjusted in the ''''Inject'''' screen: | ||
Line 5: | Line 5: | ||
[[File:02-inject.png|600px|thumb|left|Mold close and mold protection settings]] | [[File:02-inject.png|600px|thumb|left|Mold close and mold protection settings]] | ||
<br> | <br> | ||
*The | *The injection velocity can be adjusted in several ways. One can tap the ''''='''' sign to enter a constant velocity or alternatively use the up/down arrows to move the curve up and down. For more complicated injection speed profiles it is also possible to tap the curve to enter the graphical curve editor where the number of and position of individual data points can be edited. This makes it possible to make custom injection speed profiles. | ||
*The | *The 'Specific injection pressure limit' is an upper safety limit that can be set to protect the mold and/or shim (e.g. if using shims that are soft and thus prone to deformation). Note that '''this setting does not in any way ''set'' the injection pressure'''. It is only an upper safety limit that will not be exceeded. | ||
*The 'Minimum injection time' is usually set around 0-0,05 sec and 'Max. injection time' around 5-8 times the actual injection time. The actual injection time can be seen in the blueish/gray filed just over the max injection time setpoint (in this case it says 0.00 sec because no sample has been produced yet). Actual injection times are usually around 0,2 to 2 seconds so the 'Max. injection time' can typically be set to 1,0 - 15 seconds. | |||
*The | |||
Revision as of 16:37, 25 January 2018
Injection
Injection parameters are very important in injection molding optimization. The injection speed will of course determine how long time it takes to fill the cavity. It also has a large influence on the rheology of the polymer melt. Generally, viscosity of polymer melt will decrease with increasing injection speed (an effect known as shear thinning). The injection speed also influences how structures are filled and to what extent the air inside the cavity has time to escape as polymer is injected. It therefore often takes some optimization to achieve all desired sample properties. Injection speed settings are adjusted in the 'Inject' screen:
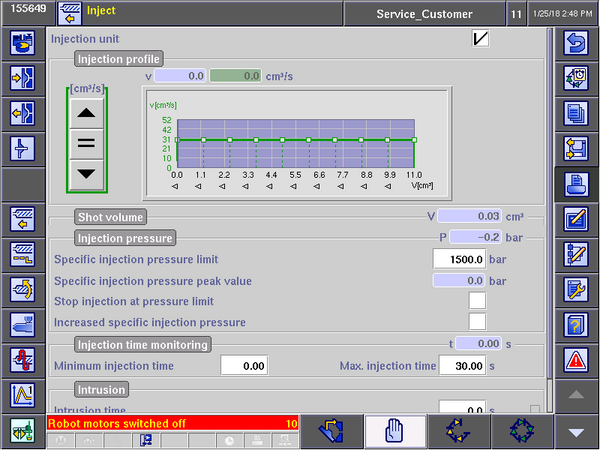
- The injection velocity can be adjusted in several ways. One can tap the '=' sign to enter a constant velocity or alternatively use the up/down arrows to move the curve up and down. For more complicated injection speed profiles it is also possible to tap the curve to enter the graphical curve editor where the number of and position of individual data points can be edited. This makes it possible to make custom injection speed profiles.
- The 'Specific injection pressure limit' is an upper safety limit that can be set to protect the mold and/or shim (e.g. if using shims that are soft and thus prone to deformation). Note that this setting does not in any way set the injection pressure. It is only an upper safety limit that will not be exceeded.
- The 'Minimum injection time' is usually set around 0-0,05 sec and 'Max. injection time' around 5-8 times the actual injection time. The actual injection time can be seen in the blueish/gray filed just over the max injection time setpoint (in this case it says 0.00 sec because no sample has been produced yet). Actual injection times are usually around 0,2 to 2 seconds so the 'Max. injection time' can typically be set to 1,0 - 15 seconds.