Specific Process Knowledge/Etch/DryEtchProcessing: Difference between revisions
Line 12: | Line 12: | ||
|-valign="top" | |-valign="top" | ||
|style="background: LightGray"| | |style="background: LightGray"| | ||
[[/Comparison| Hardware comparison]] | |[[/Comparison| Hardware comparison]] | ||
[[/Bonding| Temporary bonding]] | |[[/Bonding| Temporary bonding]] | ||
|style="background: #DCDCDC"| | |style="background: #DCDCDC"| | ||
Comparison of the different hardware setups | |Comparison of the different hardware setups | ||
Processing different sizes of substrates by bonding to carriers | |Processing different sizes of substrates by bonding to carriers | ||
|- | |- | ||
|} | |} |
Revision as of 14:29, 2 October 2014
Feedback to this page: click here
Techniques, hardware and challenges common to all dry etch tools
This page contains information that is common to dry etch instruments.
Dry etch page | Description | ||||
Hardware comparison | Temporary bonding | Comparison of the different hardware setups | Processing different sizes of substrates by bonding to carriers |
Hardware and option comparison of the dry etchers at Danchip
The table below compares the hardware and the options.
RIE2 | ASE | AOE | DRIE-Pegasus | ICP Metal etch | III-V RIE | III-V ICP | ||||||||||||||||||||||||||||||||||||||||||||||
---|---|---|---|---|---|---|---|---|---|---|---|---|---|---|---|---|---|---|---|---|---|---|---|---|---|---|---|---|---|---|---|---|---|---|---|---|---|---|---|---|---|---|---|---|---|---|---|---|---|---|---|---|
Purpose | Primary uses | The RIE chamber for etching of:
The users are allowed to have 5% metal exposed to the plasma |
Formerly the primary silicon etcher; now polymers may also be etched | Etching of silicon oxides or nitrides | Silicon etching | Standard recipes for etching of Al, Cr and Ti, now also etches of W, TiW and Mo | Etching of silicon oxide, resist, BCB, silicon nitride, InP, InGaAs and GaAs on III-V substrates | Etching of III-V materials such as GaN, InP/InGaAsP/InGaAs, AlGaAs, GaAs | ||||||||||||||||||||||||||||||||||||||||||||
Alternative/backup uses | Shallow silicon etches | Backup silicon etcher | Barc etch | Silicon etcher | ||||||||||||||||||||||||||||||||||||||||||||||||
General description | Plasma source | Parallel plate capacitor setup with RF power between the two electrodes | Inductively coupled plasma chamber with two RF generators; the coil and platen generator | Inductively coupled plasma chamber with two RF generators; the coil and platen generator | Inductively coupled plasma chamber with two RF generators; the coil (with outer and inner coil) and platen generator | Inductively coupled plasma chamber with two RF generators; the coil and platen generator | Parallel plate capacitor setup with RF power between the two electrodes | Inductively coupled plasma chamber with two RF generators; the coil and platen generator
| ||||||||||||||||||||||||||||||||||||||||||||
Substrate cooling/temperature | The electrode is oil cooled: Fixed at 20oC | The electrode is oil cooled. Also, Helium backside cooling: -10oC to 20oC | The electrode is oil cooled. Also, Helium backside cooling: -10oC to 60oC | The electrode is oil cooled. Also, Helium backside cooling: 0oC to 50oC | The electrode is oil cooled. Also, Helium backside cooling: -20oC to 30oC | The electrode is oil cooled: Fixed at 20oC | The electrode is oil cooled with a special chiller. Also, Helium backside cooling: 20oC to 180oC | |||||||||||||||||||||||||||||||||||||||||||||
Clamping | No clamping | Electrostatic clamping (semco electrode) | Electrostatic clamping (TDESC) | Electrostatic clamping (TDESC) | Electrostatic clamping (TDESC) | No clamping | Mechanical clamping (weighted clamp with ceramic fingers) | |||||||||||||||||||||||||||||||||||||||||||||
Gasses |
|
|
|
|
|
|
| |||||||||||||||||||||||||||||||||||||||||||||
RF generators |
|
|
|
|
|
|
| |||||||||||||||||||||||||||||||||||||||||||||
Substrate loading | Loading via cluster 2 load lock | Loading via dedicated two-slot carousel load lock | Loading via dedicated two-slot carousel load lock | Loading via dedicated two-slot carousel load lock or via atmospheric cassette loader | Loading via dedicated two-slot carousel load lock | Manual loading directly into process chamber | Loading via dedicated two-slot carousel load lock | |||||||||||||||||||||||||||||||||||||||||||||
Options | Optical endpoint detector at fixed wavelength |
|
|
|
|
| ||||||||||||||||||||||||||||||||||||||||||||||
Allowed materials |
|
|
|
|
|
|
|
Optical Endpoint detection systems
During a process, the plasma dissociates the gas molecules present in the process chamber into reactive species that emit light at certain wavelengths. This means that the light coming from the process chamber will be a spectrum in which elements of both process gases and process reactants are found. By analyzing the spectrum we can keep track of when certain species change concentration, i.e. when, for instance, the etch of a thin layer is complete. This is the end point of the etch hence the name.
The DRIE-Pegasus, the ICP Metal Etcher and the III-V ICP are all equipped with a Verity SD1024 Spectrometer and the SpectraView software package. The SpectraView software enables you to monitor any number of any wavelength in the 200-800 nm range and do complicated mathematical analysis of the spectra.
Setting up the OES system
Start up:
- Double click the SpectraView icon on the Verity EPD computer and the software will start.
- In the system window in the left side there is a list of configuration files. If it's not open, select View\System Window in the menu.
- Double click the configuration file you wish to use. If you need to create one that is not already there, select an existing one and save using a different name.
The configuration file: The configuration file holds the information of what to monitor; i.e. what wavelengths and what to do with their signals. To set up the configuration file you will need to know the emission wavelengths the elements or compounds you're looking for. To find this information use the help files: From the Menu go to: Help \SpectraView Manual -> Appendix D Wavelengths by emission species. It is also the intention to build up a knowledge base in LabAdviser so you may find information there as well.
The configuration file has a number of headings:
- Setup
- Usually, one should not edit this. If, however, the process is longer than 10 minutes, you will have to extend the 10 minute time out.
- Data Sources
- There is only one possible input (the optical fiber) so do not edit this.
- Regions
- Press Insert to add a region to monitor. Use an appropriate names and different colors for every region you add. For instance, call the 261.7 nm AlCl line 'AlCl_261' as name and the range og 261 to 262.5 nm, see image below. The range may be set in units of a half nanometer.
- Variables
- Only for advanced configuration files. Do not edit.
- Equations
- Determines what to do with the data from each region. Press Insert and select 'Region Equation'. Here, select
- Appropriate names and colors as with regions.
- Spectrum: Only one choice.
- Region according to name.
- Operation: Typically one will choose 'Max' to find the peak within each region, see image below. Other possibilities are Sum, Average, Min or Median.
- Snapshot
- The possibility of taking snapshots of the whole spectrum after certain time - this is not necessary.
- Graphs
- What plots to be displayed. Select
- Spectral Graphs: This will show the spectrum (typically from 200 nm to 80 nm) of light during the process.
- Trend Graphs: Select which equations to be displayed. These graphs will enable you to monitor the development of the Peaks relevant for you as you etch your sample.
- Sequence, Reprocess and Properties: Beyond the scope of this manual
Processing
Once the configuration file has been set up, it must be activated. To do so, right-click on the configuration file in the System window that you wish to use and select 'Set as Current'.
To start monitoring click one of three buttons marked by a yellow square above.
- M - Monitor
- The system will monitor the Graphs (Spectral and Trend) that have been set up in the configuration file. Panels with these Graphs will pop up. The data will not be stored. It is very useful to click the 'Tile' option under Window settings.
- C - Capture
- In addition to the monitoring described above the data will be stored on the hard drive. This enables you to analyse the data afterwards.
- P - Processing
- In addition to the monitoring and capturing of the data as described above, this mode will also feed an end point to the SPTS operator computer. It is, however, advised not to use this mode as it doesn't work for several reasons:
- It requires that an endpoint has been defined in the configuration file under 'Sequence' which is beyond the scope of this manual.
- It requires that the etch recipe on the SPTS computer has been set up for it.
Limitations
The endpoint detector may seem to be powerful tool - but it has some drawbacks. Below are listed some points that is maybe worth considering:
- The etch process parameters
- The intensity of the plasma relies heavily on process parameters such as RF powers, pressure and gas flows. It is clear that if these parameters are low, the intensity of the plasma is low and therefore the signal to noise ratio will be low.
- The intensity of the species to monitor
- The concentration of some etch product in the plasma is strongly dependent on the area that is etched. Are you etching small holes on a small chip lying on a carrier, the signal you are looking for is infinitely smaller than if you etch large areas on an entire wafer. The same applies to (high/low) etch rates.
Temporary bonding of wafers or chips for dry etching
Purpose
Many tools are set up for processing one particular size of wafer. The reasons why a tool processes one size of wafers and not others are numerous - they may include:
- Hardware availability
- Processes required by users
The dry etch tools at Danchip all have a default wafer size and may have other sizes of electrodes available. Other sizes of wafers or chips may also be processed but they will requrie the use of a carrier wafer. Using a carrier is also often required if the side of the wafer facing the electrode has structures.
Tool | Default substrate size | Alternative substrate size(s) | Sizes of wafers or chips that may bonded and processed |
---|---|---|---|
DRIE-Pegasus | 4" wafer | 6" wafer | Samples smaller than a 4" wafer |
RIE | 4" wafer | None | Samples smaller than a 4" wafer |
ASE | 4" wafer | 6" wafer | Samples smaller than a 4" wafer |
AOE | 4" wafer | None | Samples smaller than a 4" wafer |
ICP Metal Etch | 6" wafer | 4" wafer | Samples smaller than a 6" wafer |
III-V ICP | 4" wafer | None | Samples smaller than a 4" wafer |
Issues to consider
There are several issues to consider when processing a substrate that is lying (either fixed with a bonding material or lying freely) on a carrier.
- Process temperature
- The cooling of a wafer that is lying directly on the electrode is significantly more efficient than if the wafer is lying on top of a carrier. With no bonding material the wafer is essentially only touching the carrier in three points - thus drastically reducing the heat transfer to the electrode. The possible change in substrate temperature may cause the process to drift or the mask to burn away much faster. Using a bonding material such as crystal bond will increase the heat transfer between carrier and substrate.
- Process aggressiveness and material removal
- The chemical etching of materials (for instance if silicon is etched by flourine) releases energy that has to dissipated to the electrode. This release of energy depends on two factors:
- The faster the etch rate is, the more material is removed pr second, hence the more heat needs to be dissipated. This means that high power etches are much more sensible to poor heat transfer than low power processes.
- The larger area of the wafer that is etched, the more material is removed pr second. Hence, wafers with a high density of areas open for etching, will be more sensible to poor heat conductivity than wafers with little opening.
- Plasma uniformity
- The plasma will adapt to the substrate+carrier sandwich and bow along the edges of the substrate potentially disturbing the electric field that directs the ions towards the surface. This non-uniformity can be important if the substrate is very small.
Procedures
Bonding
- Find a carrier wafer that has the right size. Keep in mind that it matters a great deal if the surface will be etched or not, i.e. if it has oxide or not.
- Take a piece of crystalbond from the shelf in cleanroom 1.
- Take your items (substrate, carrier wafer, crystalbond and tweezers) to the hotplate in cleanroom 1.
- Put the carrier wafer on the hotplate. A 6" wafer will fit not in the recess but it will get sufficiently hot if you leave it there for some seconds longer.
- Apply a very thin layer of crystalbond in a circular motion so that it covers some 70 % of the area to be covered by your substrate. Do not apply too much! Little does it..
- Gently put your wafer on the crystalbond.
- Using two pairs of tweezers gently massage your substrate in a circular motion in order to distribute the crystalbond evenly between the substrate and carrier while making sure that it doesn’t get exposed on the carrier.
- If you are bonding two wafers of the same size (for instance in etch-through applications) make sure that the flats and wafer peripheries are perfectly aligned.
- Once the substrate is in the right place, cool the bonded sandwich, for instance by placing it on an aluminium block from the spinner.
- Make sure that there’s no trace of crystalbond on the backside of the carrier wafer (the side of the wafer that will face the TDESC) and you’re ready.
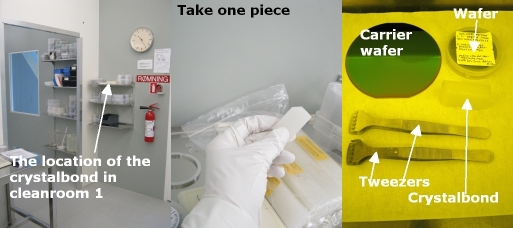
Keep in mind always to use the same kind of carrier wafer. The process conditions change dramatically if you use a blank silicon wafer instead of a wafer with a few hundred nanometers of thermal oxide when processing a, say, 2" wafer - the area of silicon exposed to plasma is quite different.
Debonding
Separating a bonded set of wafers or chips may sometimes be tricky and there is no straight forward procedure for all applications. The crystalbond dissolves in water and it melts around 65°C, so one can try one of the following procedures (that increase in aggressiveness).
- Placing the bonded sandwich on the hotplate will release the substrate. Dry with wet cleanroom cloth.
- Wash with DI water
- Wash with DI water, acetone and IPA (any photo resist on your wafer?)
- Wash with DI water, acetone and IPA and use the plasma asher