Specific Process Knowledge/Etch/Wet Polysilicon Etch: Difference between revisions
Line 7: | Line 7: | ||
The Poly Etch is typically used for opening holes in poly-silicon thin-films, using photoresist as an etch mask. Due to its isotropic nature the under-etching (etch-bias) at least amounts to the thickness of the poly-silicon layer. Another example of usage is etching of "circular-shaped" holes in silicon substrates. | The Poly Etch is typically used for opening holes in poly-silicon thin-films, using photoresist as an etch mask. Due to its isotropic nature the under-etching (etch-bias) at least amounts to the thickness of the poly-silicon layer. Another example of usage is etching of "circular-shaped" holes in silicon substrates. | ||
The | The Poly Etch is based on the combined oxidation of silicon followed by dissolution of the silicon oxide. | ||
bainitially 85 wt% H<sub>3</sub>PO<sub>4</sub> which is heated up to the boiling temperature - ca. 157 <sup>o</sup>C. Water is allowed to boil off thus raising the concentration and the boiling temperature of the solution until a boiling temperature of 180 <sup>o</sup>C is reached. Thereafter, the wafers are submerged into the bath and the water-cooled lid is closed to maintain the concentration and the boiling temperature. In some cases a lower boiling temperature is chosen - typically 160 <sup>o</sup>C - which lowers the etch rate and improves the selectivity R<sub>Si<sub>3</sub>N<sub>4</sub></sub> / R<sub>SiO<sub>2</sub></sub>. | |||
Revision as of 12:29, 30 January 2008
Wet Poly Etch
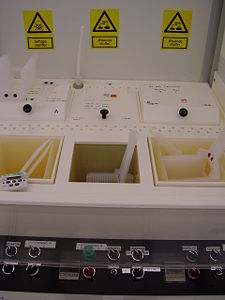
The wet Poly Etch is an isotropic silicon etch. This holds for both a poly-silicon thin-film as well as single-crystalline material such as a Si(100) surface. The Poly Etch process is placed in a dedicated PP-tank in a laminar-flow bench in cleanroom 4.
The Poly Etch is typically used for opening holes in poly-silicon thin-films, using photoresist as an etch mask. Due to its isotropic nature the under-etching (etch-bias) at least amounts to the thickness of the poly-silicon layer. Another example of usage is etching of "circular-shaped" holes in silicon substrates.
The Poly Etch is based on the combined oxidation of silicon followed by dissolution of the silicon oxide.
bainitially 85 wt% H3PO4 which is heated up to the boiling temperature - ca. 157 oC. Water is allowed to boil off thus raising the concentration and the boiling temperature of the solution until a boiling temperature of 180 oC is reached. Thereafter, the wafers are submerged into the bath and the water-cooled lid is closed to maintain the concentration and the boiling temperature. In some cases a lower boiling temperature is chosen - typically 160 oC - which lowers the etch rate and improves the selectivity RSi3N4 / RSiO2.
NB: Great care has to be taken in this process due to risk of "shock-boiling"
Nitride etch - key facts
Nitride etch @ 180 oC | Nitride etch @ 160 oC | |
---|---|---|
General description |
Etch/strip of silicon nitride |
Etch/strip of silicon nitride |
Chemical solution | H3PO4 (85 wt%) | H3PO4 (85 wt%) |
Process temperature | 180 oC | 160 oC |
Possible masking materials: |
|
|
Etch rate |
|
|
Batch size |
1-25 wafers at a time |
1-25 wafer at a time |
Size of substrate |
2-6" wafers |
2-6" wafers |