Specific Process Knowledge/Etch/Wet Polysilicon Etch: Difference between revisions
Line 3: | Line 3: | ||
[[Image:Wet_PolySi_etch.jpg|300x300px|thumb|Wet PolySilicon Etch (in the middle): positioned in cleanroom 4]] | [[Image:Wet_PolySi_etch.jpg|300x300px|thumb|Wet PolySilicon Etch (in the middle): positioned in cleanroom 4]] | ||
The wet Poly Etch is an isotropic silicon etch. This holds for both a poly-silicon thin-film as well as single-crystalline material such as a Si(100) surface. The Poly Etch process is placed in a dedicated PP-tank in cleanroom 4. | The wet Poly Etch is an isotropic silicon etch. This holds for both a poly-silicon thin-film as well as single-crystalline material such as a Si(100) surface. The Poly Etch process is placed in a dedicated PP-tank in a laminar-flow bench in cleanroom 4. | ||
The Poly Etch is typically used for opening holes in poly-silicon thin-films, using photoresist as an etch mask. Due to its isotropic nature the under-etching (etch-bias) at least amounts to the thickness of the poly-silicon layer. Another example of usage is etching of "circular-shaped" holes in silicon substrates. | |||
The process is mainly used to strip silicon nitride (maskless), but can also be used for masked etching of silicon nitride using some kind of silicon oxide as etch mask. However, the wet silicon nitride etch is isotropic meaning that the under-etching (etch-bias) at least amounts to the thickness of the silicon nitride layer. | |||
The etch solution is initially 85 wt% H<sub>3</sub>PO<sub>4</sub> which is heated up to the boiling temperature - ca. 157 <sup>o</sup>C. Water is allowed to boil off thus raising the concentration and the boiling temperature of the solution until a boiling temperature of 180 <sup>o</sup>C is reached. Thereafter, the wafers are submerged into the bath and the water-cooled lid is closed to maintain the concentration and the boiling temperature. In some cases a lower boiling temperature is chosen - typically 160 <sup>o</sup>C - which lowers the etch rate and improves the selectivity R<sub>Si<sub>3</sub>N<sub>4</sub></sub> / R<sub>SiO<sub>2</sub></sub>. | The etch solution is initially 85 wt% H<sub>3</sub>PO<sub>4</sub> which is heated up to the boiling temperature - ca. 157 <sup>o</sup>C. Water is allowed to boil off thus raising the concentration and the boiling temperature of the solution until a boiling temperature of 180 <sup>o</sup>C is reached. Thereafter, the wafers are submerged into the bath and the water-cooled lid is closed to maintain the concentration and the boiling temperature. In some cases a lower boiling temperature is chosen - typically 160 <sup>o</sup>C - which lowers the etch rate and improves the selectivity R<sub>Si<sub>3</sub>N<sub>4</sub></sub> / R<sub>SiO<sub>2</sub></sub>. |
Revision as of 12:25, 30 January 2008
Wet Poly Etch
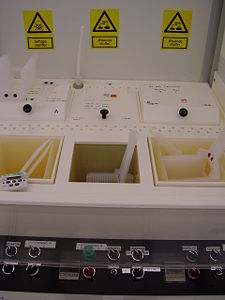
The wet Poly Etch is an isotropic silicon etch. This holds for both a poly-silicon thin-film as well as single-crystalline material such as a Si(100) surface. The Poly Etch process is placed in a dedicated PP-tank in a laminar-flow bench in cleanroom 4.
The Poly Etch is typically used for opening holes in poly-silicon thin-films, using photoresist as an etch mask. Due to its isotropic nature the under-etching (etch-bias) at least amounts to the thickness of the poly-silicon layer. Another example of usage is etching of "circular-shaped" holes in silicon substrates.
The process is mainly used to strip silicon nitride (maskless), but can also be used for masked etching of silicon nitride using some kind of silicon oxide as etch mask. However, the wet silicon nitride etch is isotropic meaning that the under-etching (etch-bias) at least amounts to the thickness of the silicon nitride layer.
The etch solution is initially 85 wt% H3PO4 which is heated up to the boiling temperature - ca. 157 oC. Water is allowed to boil off thus raising the concentration and the boiling temperature of the solution until a boiling temperature of 180 oC is reached. Thereafter, the wafers are submerged into the bath and the water-cooled lid is closed to maintain the concentration and the boiling temperature. In some cases a lower boiling temperature is chosen - typically 160 oC - which lowers the etch rate and improves the selectivity RSi3N4 / RSiO2.
NB: Great care has to be taken in this process due to risk of "shock-boiling"
Nitride etch - key facts
Nitride etch @ 180 oC | Nitride etch @ 160 oC | |
---|---|---|
General description |
Etch/strip of silicon nitride |
Etch/strip of silicon nitride |
Chemical solution | H3PO4 (85 wt%) | H3PO4 (85 wt%) |
Process temperature | 180 oC | 160 oC |
Possible masking materials: |
|
|
Etch rate |
|
|
Batch size |
1-25 wafers at a time |
1-25 wafer at a time |
Size of substrate |
2-6" wafers |
2-6" wafers |