Specific Process Knowledge/Etch/KOH Etch: Difference between revisions
Line 2: | Line 2: | ||
[[Image:KOH_4tommer.jpg|300x399px|thumb|KOH etch for 4" wafers: positioned in cleanroom 3]] | [[Image:KOH_4tommer.jpg|300x399px|thumb|KOH etch for 4" wafers: positioned in cleanroom 3]] | ||
KOH belongs to the family of anisotropic Si-etchants based on aqueous alkaline solutions. The anisotropy stems from the different etch rates in different crystal directions. The {111}-planes are almost inert whereas the etch rates of e.g. {100}- and {110}-planes are several orders of magnitude faster. | KOH belongs to the family of anisotropic Si-etchants based on aqueous alkaline solutions. The anisotropy stems from the different etch rates in different crystal directions. The {111}-planes are almost inert whereas the etch rates of e.g. {100}- and {110}-planes are several orders of magnitude faster. | ||
KOH-etching is a highly versatile and cheap way to realize micromechanical structures if you can live with the necessary Si<math>_3</math>N<math>_4</math>- or SiO<math>_2</math> masking materials and the K contamination of the surface. | |||
At Danchip we use as a standard a 28 wt% KOH. The etch rate - and the selectivity towards a SiO<math>_2</math>-mask - is depending on the temperature. We normally use T=80 <sup>o</sup>C but may choose to reduce this to e.g. 60 <sup>o</sup>C or 70 <sup>o</sup>C in case of a high-precission timed etch (e.g. defining a thin membrane). In some cases we recommend to saturate the standard 28 wt% KOH with IPA with an etch temperature at T=70 <sup>o</sup>C (reduce evaporation of IPA). One example is for boron etch-stop, where the selectivity towards the boron-doped silicon is improved roughly a factor of 10 compared to the standard etch. Key facts for the two solutions are resumed in the table: | At Danchip we use as a standard a 28 wt% KOH. The etch rate - and the selectivity towards a SiO<math>_2</math>-mask - is depending on the temperature. We normally use T=80 <sup>o</sup>C but may choose to reduce this to e.g. 60 <sup>o</sup>C or 70 <sup>o</sup>C in case of a high-precission timed etch (e.g. defining a thin membrane). In some cases we recommend to saturate the standard 28 wt% KOH with IPA with an etch temperature at T=70 <sup>o</sup>C (reduce evaporation of IPA). One example is for boron etch-stop, where the selectivity towards the boron-doped silicon is improved roughly a factor of 10 compared to the standard etch. Key facts for the two solutions are resumed in the table: |
Revision as of 12:12, 28 January 2008
KOH etch - Anisotropic silicon etch
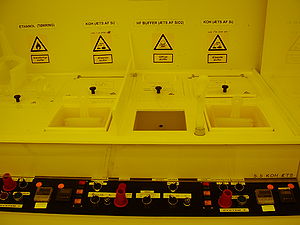
KOH belongs to the family of anisotropic Si-etchants based on aqueous alkaline solutions. The anisotropy stems from the different etch rates in different crystal directions. The {111}-planes are almost inert whereas the etch rates of e.g. {100}- and {110}-planes are several orders of magnitude faster.
KOH-etching is a highly versatile and cheap way to realize micromechanical structures if you can live with the necessary SiN- or SiO masking materials and the K contamination of the surface.
At Danchip we use as a standard a 28 wt% KOH. The etch rate - and the selectivity towards a SiO-mask - is depending on the temperature. We normally use T=80 oC but may choose to reduce this to e.g. 60 oC or 70 oC in case of a high-precission timed etch (e.g. defining a thin membrane). In some cases we recommend to saturate the standard 28 wt% KOH with IPA with an etch temperature at T=70 oC (reduce evaporation of IPA). One example is for boron etch-stop, where the selectivity towards the boron-doped silicon is improved roughly a factor of 10 compared to the standard etch. Key facts for the two solutions are resumed in the table:
Comparing the two solutions
28 wt% KOH | 28 wt% KOH sat. with IPA | |
---|---|---|
General description |
Etch of Si(100) |
Etch of Si(100) with boron etch-stop |
Chemical solution | HO:HPO 1:2 | PES 77-19-04 |
Process temperature | 50 oC | 20 oC |
Possible masking materials: |
Photoresist (1.5 µm AZ5214E) |
Photoresist (1.5 µm AZ5214E) |
Etch rate |
~100 nm/min (Pure Al) |
~60(??) nm/min |
Batch size |
1-25 wafers at a time |
1-25 wafer at a time |
Size of substrate |
4" wafers |
4" wafers |
Allowed materials |
|
|