Specific Process Knowledge/Lithography/EBeamLithography: Difference between revisions
Line 256: | Line 256: | ||
[[Image:GlobalMark.png|200px|thumb|]] | [[Image:GlobalMark.png|200px|thumb|]] | ||
A set of global marks are needed in order to align an exposure to an existing pattern on a wafer. These marks should be clearly visible in a 100keV SEM, i.e. preferably defined by Ti/Au or another 'heavy' metal. Etched global marks or global marks defined by a light metal as Al can be hard to locate manually as well as automatically. | |||
The global marks should either be crosses or L-shaped and be quite large, i.e. 500 - 1000 microns in length. If the wafer contains a number of identical marks, the marks should be marked in order to identify the 'right' alignment marks (the scan width of the SEM is 1 mm x 1 mm). | |||
The marks should be as narrow as possible. | |||
Global marks formed as crosses with lengths of 1000 microns and 3-5 microns in width are recommended. | |||
= Proximity Error Correction = | = Proximity Error Correction = |
Revision as of 13:51, 23 April 2014
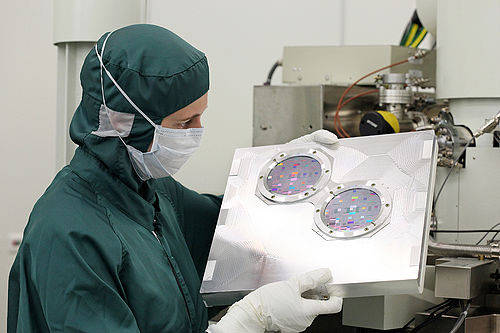
Feedback to this page: click here
The JEOL JBX-9500 electron beam lithography system is a spot electron beam type lithography system designed for writing patterns with dimensions from nanometers to sub-micrometers. The minimum electron beam is around 12 nm, the maximum writitng field without stitching is 1 mm x 1 mm.
The machine is located in a class 10 cleanroom (E-2) with tight temperature and moisture control. The room must only be entered when the machines or equipment inside the room is intended to be used.
The user manual, technical information and contact information can be found in LabManager:
Performance of the e-beam writer
Purpose | pattern an electron sensitive resist | Mainly for pattering structures with minimum feature size between 12 nm - 1 µm |
---|---|---|
Performance | Resolution |
|
Maximum writing area without stitching |
| |
Process parameter range | E-beam voltage |
|
Scanning speed |
| |
Min. electron beam size |
| |
Min. step size |
| |
Beam current range |
| |
Dose range |
| |
Samples | Batch size |
Wafer cassettes:
|
Substrate material allowed |
|
Getting started
Request for training on machine
To request for an e-beam training session, contact e-beam@danchip.dtu.dk; a DTU Danchip personnel will hereafter provide a time slot. Users require at least 4 training sessions before being allowed full acccess to the machine. The first training will focus on file preparation and compilation alone.
Before you request for a training, it is crucial to have your pattern ready in either tdb-format or GDSII format. Also, check your pattern in e.g. CleWin before requesting. In order to reach the files from the computers inside the cleanroom, it is recommended to either dropbox them or send them per email to yourself.
It is also recommended to gather as much knowledge about your e-beam run from your colleagues, i.e. which e-beam current, aperture and dose to use, which shot pitch (e.g. SHOT A,10). In order to get an overview of what an e-beam process requires, it is recommended to a assist a fully trained colleague of yours when she or he e-beam writes. Furthermore, please read the e-beam manual for more information on which parameters to use.
On the L-drive, a logbook for the e-beam writer can be found. Sheet 1 gives you an overview of which condition files (currents and apertures) have been in use recently by which user on which type of resist. On sheet 2 in this logbook you can find a writing time estimation program. Please, consult this logbook prior to requesting e-beam training sessions. If in doubt how to use it, contact the e-beam team at e-beam@danchip.dtu.dk.
General Rules
For safety reasons, even fully trained users are only authorized to mount substrates into the e-beam cassettes, but not authorized to load the cassettes into the autoloader.
There are two daily loading sessions where cassettes will be loaded into the autoloader by DTU Danchip personel:
- 10:00 - 10:30
- 13:30 - 14:00
To use the e-beam writer, book the machine via LabManager, show up to the loading session before your exposure to mount your substrate and pre-align if necessary.
After your exposure, fully trained users can unload their cassettes from the autoloader, unmount their substrates and re-load an empty cassette into the autoloader. If you are prohibited to unmount your substrates before another user requires the cassette, you must accept that either the next user or DTU Danchip personel unmount your substrates.
Manuals
There are 3 manuals for the e-beam writer:
- A user manual describing the standard procedure when e-beam writing
- A jdf-, and sdf-file manual describing how to prepare sdf-, and jdf-files (found under 'Technical Documents')
- A BEAMER manual describing how to convert your pattern file (GDSII-format) to v30-format (found under 'Technical Documents')
E-beam resists and Process Flows
The table describes the e-beam resist used in the cleanroom for standard e-beam exposure. Some of resists are not provided by DTU Danchip and some are not yet approved for common use in the cleanroom and are currently being tested. If you wish to test some of these resists or other resists, please contact Lithography.
Resist | Polarity | Manufacturer | Comments | Technical reports | Spinner | Developer | Rinse | Remover | Process flows (in docx-format) |
ZEP520A | Positive | ZEON | Standard positive resist | ZEP520A.pdf, Spin curves for ZEP520A on SSE Spinner | SSE, Manual Spinner 1 (Laurell), III-V Spinner | ZED-N50/Hexyl Acetate,n-amyl acetate, oxylene. JJAP-51-06FC05.pdf, JVB001037.pdf | IPA | acetone/1165 | Process_Flow_ZEP.docx, Process_Flow_ZEP_with_Al.docx |
CSAR | Positive | AllResist | Approved, not tested yet. Should work similar to ZEP520A. Please contact Lithography for information. | CSAR_62_and_process_chemicals.pdf, CSAR_62_Abstract_Allresist.pdf | Manual Spinner 1 (Laurell), III-V Spinner | X AR 600-54/6, MIBK:IPA | IPA, H2O | Process_Flow_CSAR.docx | |
ZEP7000 | Positive | ZEON | Not approved and not yet purchased. Low dose to clear, can be used for trilayer (PEC-free) resist-stack. Please contact Lithography for information. | ZEP7000.pdf | Manual Spinner 1 (Laurell), III-V Spinner | ZED-500/Hexyl Acetate,n-amyl acetate, oxylene. | IPA | acetone/1165 | Trilayer stack: Process_Flow_Trilayer_Ebeam_Resist.docx |
PMMA | Positive | We have various types of PMMA in the cleanroom, none are provided by DTU Danchip. Please contact Lithography for information. | Manual Spinner 1 (Laurell), III-V Spinner | MIBK:IPA (1:3), IPA:H2O | IPA | acetone/1165/Pirahna | |||
MMA (AR-P 617.05) | Positive | AllResist | Approved, not tested yet. Used for trilayer (PEC-free) resist-stack or double-layer lift-off resist stack. Please contact Lithography for information. | AR_P617.pdf | Manual Spinner 1 (Laurell), III-V Spinner | AR600-55, MIBK:IPA | acetone/1165 | Trilayer stack: Process_Flow_Trilayer_Ebeam_Resist.docx
| |
HSQ (XR-1541) | Negative | DOW Corning | Approved. Standard negative resist, mainly for III-V materials | III-V Spinner | TMAH, AZ400K:H2O | H2O |
| ||
ma-N 2403 | Negative | Micro Resist | Approved. Standard negative resist. | III-V Spinner | Ma-D333, TMAH, MIF726 | H2O | acteone/O2 plasma | ||
AR-N 7520 | Negative | AllResist | Both e-beam, DUV and UV-sensitive resist. Currently being tested, contact Peixiong Shi for information. | AR-N7500-7520.pdf | Manual Spinner 1 (Laurell), III-V Spinner |
|
Alignment of exposure to existing pattern on wafer
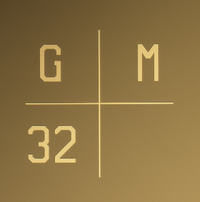
A set of global marks are needed in order to align an exposure to an existing pattern on a wafer. These marks should be clearly visible in a 100keV SEM, i.e. preferably defined by Ti/Au or another 'heavy' metal. Etched global marks or global marks defined by a light metal as Al can be hard to locate manually as well as automatically.
The global marks should either be crosses or L-shaped and be quite large, i.e. 500 - 1000 microns in length. If the wafer contains a number of identical marks, the marks should be marked in order to identify the 'right' alignment marks (the scan width of the SEM is 1 mm x 1 mm).
The marks should be as narrow as possible.
Global marks formed as crosses with lengths of 1000 microns and 3-5 microns in width are recommended.
Proximity Error Correction
Even though the electron beam diameter is below 5 nm, the feature and pitch resolution in resist is limited by the forward and backward scattering of the electrons. The forward scattering depends on the electron acceleration voltage, the resist material and thickness. The backward scattering depends on the electron acceleration voltage and the substrate material [1], [2].
As the travel distance of backscattered electrons is fairly large, e-beam patterned structures will be influenced by adjacent e-beam patterned structures, i.e. a proximity effect. These proximity effects can be avoided either by simulating a proximity error correction (PEC) in BEAMER or by using the right stack of e-beam resist.
Proximity Error Correction (PEC) in BEAMER
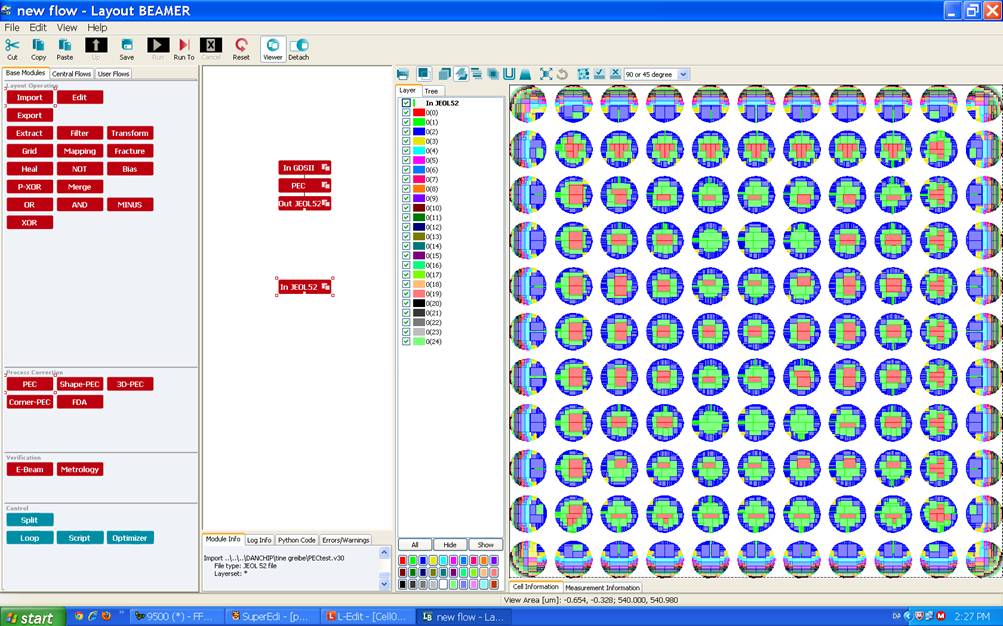
BEAMER is endowed with a software that corrects for proximity errors in the e-beam exposure. You can ready more about this function in the BEAMER manual in LabManager under Technical Documents here and in the BEAMER presentation here BEAMERPresentation.pdf.
The proximity error correction require a forward and a backward range parameter, alfa and beta, and a ratio of backscattered energy to the forward scattered energy, eta. As alfa depends on the electron acceleration voltage, which is constant at 100kV, alfa is in BEAMER fixed to 0.007. Help to find beta and eta can be found here.
Alternatively, a point-spread function can be used in BEAMER to calculate the optimised dose-variation.
Trilayer resist stack
As an alternative to PEC, a trilayer reists stack with a thin layer of thermally evaporated Ge can be used [3]. This reists stack has not yet been tested at DTU Danchip. A process flow for this procedure can be found here Process_Flow_Trilayer_Ebeam_Resist.docx, but please contact Lithography before use.
Charging of non-conductive substrates and height measurements on transparent substrates
All substrates are grounded to the cassette when proper loaded. In a non-conducting substrate, the accumulation of charges in the substrates will however destroy the e-beam patterning. To avoid this, a charge dissipating layer is added on top of the e-beam resist; this will provide a conducting layer for the electrons to escape, while high-energy electrons will pass through the layer to expose the resist.
Also, some substrates are transparent for the substrate height detector; a 20 nm Aluminum coating is recommended on these substrates.
If you wish to investigate the charge dissipation using other methods than below, please contact Lithography.
Aluminum coating
At DTU Danchip, we recommend to use a thin (20 nm) layer of thermally evaporated aluminum on top of the e-beam resist. Preferably, the thickness of Al and the e-beam dose should be optimised to the features you wish to e-beam pattern, e.g. [4]. The 20 nm Al seems as a good starting point wherefrom dose and development can be optimised to reach the resolution and feature size required.
The process flow for a standard e-beam exposure on ZEP520 with Al on top can be found here Process_Flow_ZEP_with_Al.docx.
ESPACER
We have ESPACER in stock and approved for use in the cleanroom but have not yet had the chance to investigate the material. You can find a guideline for a process flow here: Process_Flow_ZEP_ESPACER.docx. Technical information of EPSCAER can be found here: Espacer_300_Technical_Info.pdf, Espacer_catalog.pdf.
Please contact Lithography if you wish to test this material.