Specific Process Knowledge/Thermal Process/Annealing: Difference between revisions
No edit summary |
|||
Line 1: | Line 1: | ||
=<span style="background:#FF2800">THIS PAGE IS UNDER CONSTRUCTION</span>[[image:Under_construction.png|200px]]= | |||
'''Feedback to this page''': '''[mailto:labadviser@danchip.dtu.dk?Subject=Feed%20back%20from%20page%20http://labadviser.danchip.dtu.dk/index.php/Specific_Process_Knowledge/Thermal_Process/Annealing click here]''' | '''Feedback to this page''': '''[mailto:labadviser@danchip.dtu.dk?Subject=Feed%20back%20from%20page%20http://labadviser.danchip.dtu.dk/index.php/Specific_Process_Knowledge/Thermal_Process/Annealing click here]''' | ||
Revision as of 09:59, 18 March 2014
THIS PAGE IS UNDER CONSTRUCTION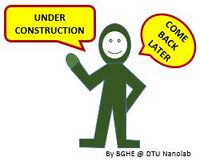
Feedback to this page: click here
Annealing
At Danchip we have seven furnaces and an RTP for annealing: A1, A3, C1, C2, C3, C4, noble furnace and RTP. Annealing normally takes place in an N2 atmosphere. PECVD PBSG is annealed in an wet atmosphere which will also oxidize the silicon substrate.
- Anneal with N2 can be done in furnaces:A1,A3,C1,C2,C3,C4, noble furnace and RTP
- Wet anneal with H2O in a bubbler can be done in furnaces:C1 and C3.
Comparison of the seven annealing equipments
A1 Boron drive-in |
A3 Phosphorous drive-in |
C1 Anneal oxide |
C3 Anneal bond |
C4 Anneal aluminium |
Nobel furnace | RTP | |
General description | Drive-in of boron deposited in the boron pre-dep furnace(A2) or drive-in of ion implanted boron. Can also be used for oxidation. | Drive-in of phosphorous deposited in the phosphorous pre-dep furnace(A2) or drive-in of ion implanted phosphorous. Can also be used for oxidation. | Annealing and oxidation of wafers from the B-stack and PECVD1. At the moment also used for general annealing and oxidation of 6" wafers. | Annealing and oxidation of wafers from NIL. | Annealing of wafers with aluminium. | Annealing and oxidation of any material. | Rapid thermal annealing. |
---|---|---|---|---|---|---|---|
Annealing with N2 | x | x | x | x | x | x | x |
Wet annealing with bubler (water steam + N2) | . | . | x | x | . | . | . |
Process temperature [ oC ] | 800-1150 | 800-1150 | 800-1150 | 800-1150 | 800-1150 | 22-1000oC | 22-1000oC |
Batch size | max. 30 wafers of 4" or 2" | max. 30 4" wafers or 2" wafers | max. 30 wafers of 6",4" or 2" | max. 30 4" wafers or 2" wafers | max. 30 4" wafers or 2" wafers | 30x4" or small pieces | 1x4" or small pieces |
Which wafers are allowed to enter the furnace: | A1 Boron drive-in |
A3 Phosphorous drive-in |
C1 Anneal oxide |
C3 Anneal bond |
C4 Anneal aluminium |
Nobel | RTP |
New clean* Si wafers 4" (6" in C1) | . | . | . | x | x | x | x |
RCA clean** Si wafers with no history of Metals on | x | x | x | x | x | x | x |
From Predep furnace directly (e.g. incl. Predep HF**) | From A2 | From A4 | x | x | x | x | x |
Wafers directly from PECVD1 | . | . | x | x | x | x | x |
Wafers directly from NIL bonding | . | . | . | x | x | x | x |
Wafers with aluminium | . | . | . | . | x | x | . |
wafers with other metals | . | . | . | . | x | . | |
wafers with III-V materials | x |
*New clean: only right from the new clean box. It is not allowed to put them in another box first.
**These wafers must be placed in a "transport box from RCA to furnace" using the RCA carrier when doing RCA or the pre-dep carrier after pre-dep.
Comparison of the seven oxidation furnaces
Generel description | Drive-in of boron deposited in the boron pre-dep furnace(A1) or drive-in of ion implanted boron. Can also be used for dry and wet oxidation. | Oxidation of gate-oxide and other especially clean oxides. | Drive-in of phosphorous deposited in the phosphorous pre-dep furnace(A4) or drive-in of ion implanted phosphorous. Can also be used for dry and wet oxidation. | Oxidation and annealing of 6" wafers. Oxidation of new wafer with out RCA cleaning. Annealing of wafers from the LPCVD furnaces and PECVD1. | Oxidation and annealing of wafers from EVG-NIL, PECVD3 and wafers with aluminum. | Oxidation of very thick oxides, thickness higher than 4 µm. | Oxidation and annealing of almost materials on silicon wafer. |
---|---|---|---|---|---|---|---|
Oxidation method |
|
|
|
|
|
|
|
Annealing gas |
|
|
|
|
|
|
|
Process temperatur |
|
|
|
|
|
|
|
Substrate and Batch size |
Including one test wafer |
Including one test wafer |
Including one test wafer |
Including one test wafer |
Including one test wafer |
|
|
Allowed materials |
All wafers have to be RCA cleaned. Except for Boron pre-dep wafer from furnace A1. |
All wafers have to be RCA cleaned. |
All wafers have to be RCA cleaned. Except for Phosphorous pre-dep wafers from furnace A4. |
All processed wafers have to be RCA cleaned. Except for wafers from LPCVD furnace and PECVD1. |
All wafers have to be RCA cleaned. Except for wafers from EVG-NIL, PECVD3 and wafer for annealing of aluminum. |
Only new wafers |
Almost all meterials |