Specific Process Knowledge/Thin film deposition/Deposition of Nickel/Electroplating of nickel: Difference between revisions
No edit summary |
|||
(21 intermediate revisions by 3 users not shown) | |||
Line 1: | Line 1: | ||
Electroplating of nickel: | Electroplating of nickel: DTU Nanolab standard processes | ||
'''Feedback to this page''': '''[mailto: | '''Feedback to this page''': '''[mailto:fabricationSupport@anolab.dtu.dk?Subject=Feed%20back%20from%20page%20http://labadviser.nanolab.dtu.dk/index.php?title=Specific_Process_Knowledge/Thin_film_deposition/Deposition_of_Nickel/Electroplating_of_nickel click here]''' | ||
''Unless anything else is stated, everything on this page, text and pictures are made by DTU Nanolab.'' | |||
<span style="color:Red">'''THIS EQUIPMENT HAS BEEN DECOMMISSIONED, Spring 2023.''' </span> | |||
'''For electroplating, please contact DTU Mechanical Engineering.''' | |||
<br clear="all" /> | <br clear="all" /> | ||
== | == DTU Nanolab Standard Programs == | ||
Three different standard programs have been made by DTU Nanolab. They have all been made to fabricate nickel shims for use in the polymer injection molding machine at DTU Nanolab. For this purpose a nickel thickness of around 340-360 µm is optimal. By experimentation it has been found that the required charge for this sample thickness is 18,3 Ah. The only difference between the different standard programs is the time required for depositing the nickel. The three different standard programs deposit the ~350 µm of nickel in about 4, 6 or 12 hours respectively. | |||
The following figure shows the current profile during the first 2 hours of the programs: | The following figure shows the current profile during the first 2 hours of the programs: | ||
[[Image: | [[Image:CurrentProfiles2019.png|center|Current profiles of standard programs]] | ||
As can be seen from the illustration the first 30 minutes of all standard processes are identical. All processes use a slow ramping of the current. This is to make sure that some material is deposited which can conduct a higher current. Starting a plating process at several amperes is very likely to damage the sample (and possibly the sample holder) because the seed metal layer (usually 50-120 nm thick) cannot support such high currents. | |||
The Standard programs are named using the following convention: '''DCHimmXX.X-YY''' where '''DCH''' indicates it's a process developed by Nanolab, '''imm''' that is a process developed for producing samples for the '''i'''njection '''m'''olding '''m'''achine, '''XX.X''' denotes the charge in Ah (Ampere-hours) and '''YY''' denotes the approximate process time in hours. | |||
<br clear="all" /> | <br clear="all" /> | ||
Line 23: | Line 31: | ||
|-style="background:silver; color:black" | |-style="background:silver; color:black" | ||
! | ! | ||
![[Specific_Process_Knowledge/Thin_film_deposition/Deposition_of_Nickel/Electroplating_of_nickel|DCHimm18- | ![[Specific_Process_Knowledge/Thin_film_deposition/Deposition_of_Nickel/Electroplating_of_nickel|DCHimm18.3-04]] | ||
![[Specific_Process_Knowledge/Thin_film_deposition/Deposition_of_Nickel/Electroplating_of_nickel|DCHimm18- | ![[Specific_Process_Knowledge/Thin_film_deposition/Deposition_of_Nickel/Electroplating_of_nickel|DCHimm18.3-06]] | ||
![[Specific_Process_Knowledge/Thin_film_deposition/Deposition_of_Nickel/Electroplating_of_nickel|DCHimm18- | ![[Specific_Process_Knowledge/Thin_film_deposition/Deposition_of_Nickel/Electroplating_of_nickel|DCHimm18.3-12]] | ||
![ | |- | ||
|- | |||
|-style="background:WhiteSmoke; color:black" | |||
!Charge [Ah] | |||
|18,3 | |||
|18,3 | |||
|18,3 | |||
|- | |- | ||
|- | |- | ||
|-style="background:WhiteSmoke; color:black" | |-style="background:WhiteSmoke; color:black" | ||
!Expected nickel thickness | !Expected nickel thickness | ||
| | |350 µm | ||
| | |350 µm | ||
| | |350 µm | ||
|- | |- | ||
|- | |- | ||
|-style="background:LightGrey; color:black" | |-style="background:LightGrey; color:black" | ||
!Maximum current [A] | !Maximum current [A] | ||
| | | | ||
5,5 | 5,5 | ||
Line 55: | Line 64: | ||
!Process time [hh:mm:ss] | !Process time [hh:mm:ss] | ||
| | | | ||
04:10:55 | |||
| | | | ||
06:12:52 | |||
| | | | ||
12: | 12:28:01 | ||
|- | |- | ||
|- | |- | ||
|-style="background:LightGrey; color:black" | |-style="background:LightGrey; color:black" | ||
! | !Process comments | ||
| | | | ||
A fast program that allows one to produce two samples in a normal working day. Usually works fine for rapid prototyping. | |||
| | | | ||
A compromise between desired material properties (hardness, ductility, roughness) and process time. Will result in a sample that will be useful for most standard injection molding processes. | |||
| | | | ||
A slower process that in return results in lower roughness and stronger mechanical properties. A good choice for shims that will be used with 'harsh' injection molding parameters (high temperatures and high pressures). | |||
|- | |- | ||
|} | |} | ||
<br clear="all" /> | <br clear="all" /> |
Latest revision as of 10:37, 9 June 2023
Electroplating of nickel: DTU Nanolab standard processes
Feedback to this page: click here
Unless anything else is stated, everything on this page, text and pictures are made by DTU Nanolab.
THIS EQUIPMENT HAS BEEN DECOMMISSIONED, Spring 2023.
For electroplating, please contact DTU Mechanical Engineering.
DTU Nanolab Standard Programs
Three different standard programs have been made by DTU Nanolab. They have all been made to fabricate nickel shims for use in the polymer injection molding machine at DTU Nanolab. For this purpose a nickel thickness of around 340-360 µm is optimal. By experimentation it has been found that the required charge for this sample thickness is 18,3 Ah. The only difference between the different standard programs is the time required for depositing the nickel. The three different standard programs deposit the ~350 µm of nickel in about 4, 6 or 12 hours respectively.
The following figure shows the current profile during the first 2 hours of the programs:
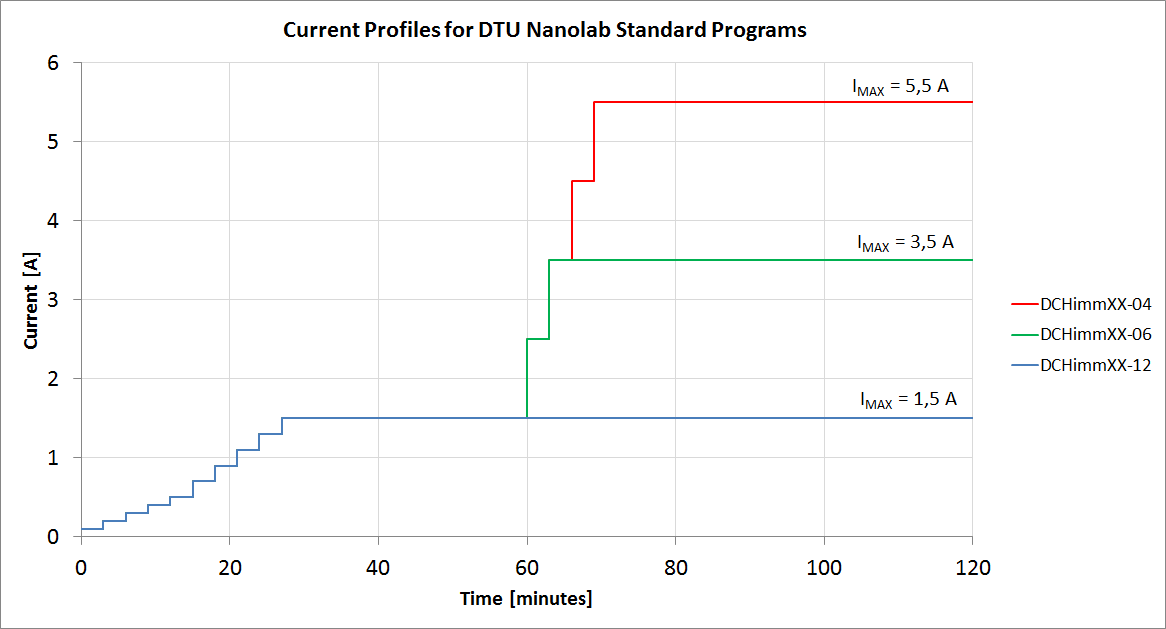
As can be seen from the illustration the first 30 minutes of all standard processes are identical. All processes use a slow ramping of the current. This is to make sure that some material is deposited which can conduct a higher current. Starting a plating process at several amperes is very likely to damage the sample (and possibly the sample holder) because the seed metal layer (usually 50-120 nm thick) cannot support such high currents.
The Standard programs are named using the following convention: DCHimmXX.X-YY where DCH indicates it's a process developed by Nanolab, imm that is a process developed for producing samples for the injection molding machine, XX.X denotes the charge in Ah (Ampere-hours) and YY denotes the approximate process time in hours.
Comparison of standard processes
DCHimm18.3-04 | DCHimm18.3-06 | DCHimm18.3-12 | |
---|---|---|---|
Charge [Ah] | 18,3 | 18,3 | 18,3 |
Expected nickel thickness | 350 µm | 350 µm | 350 µm |
Maximum current [A] |
5,5 |
3,5 |
1,5 |
Process time [hh:mm:ss] |
04:10:55 |
06:12:52 |
12:28:01 |
Process comments |
A fast program that allows one to produce two samples in a normal working day. Usually works fine for rapid prototyping. |
A compromise between desired material properties (hardness, ductility, roughness) and process time. Will result in a sample that will be useful for most standard injection molding processes. |
A slower process that in return results in lower roughness and stronger mechanical properties. A good choice for shims that will be used with 'harsh' injection molding parameters (high temperatures and high pressures). |