Specific Process Knowledge/Characterization/PL mapper: Difference between revisions
No edit summary |
|||
(6 intermediate revisions by the same user not shown) | |||
Line 3: | Line 3: | ||
==PhotoLuminescence Mapper RPM2000 == | ==PhotoLuminescence Mapper RPM2000 == | ||
[[Image:PL-mapper.jpg|500px|right|thumb|Positioned in the MOCVD room: F-1]] | [[Image:PL-mapper.jpg|500px|right|thumb|Positioned in the MOCVD room: F-1, {{photo1}}]] | ||
{{CC1}}<br> | |||
Photoluminescence mapping is a non-contact, non-destructive technique for mapping out uniformity of alloy composition, material quality and defects in substrates and of III-V epiwafers. The Rapid Photoluminiscence Mapper (RPM) is equipped with 3 lasers for PL measurements and a white-light source to map out thickness and reflectance of eg layers, microcavities and VCSELs. | Photoluminescence mapping is a non-contact, non-destructive technique for mapping out uniformity of alloy composition, material quality and defects in substrates and of III-V epiwafers. The Rapid Photoluminiscence Mapper (RPM) is equipped with 3 lasers for PL measurements and a white-light source to map out thickness and reflectance of eg layers, microcavities and VCSELs. | ||
[[Image:Wafer-bonding PL-mapper (LabAdviser) Jehem.jpg|500px|right|thumb|Map of two bonded silicon wafers. Red areas are voids between the wafers]] | [[Image:Wafer-bonding PL-mapper (LabAdviser) Jehem.jpg|500px|right|thumb|Map of two bonded silicon wafers. Red areas are voids between the wafers, Made by Jens Hemmingsen @ DTU Nanolab]] | ||
It can also be used to map out voids after silicon wafer-bonding. This is done using the reflectance mapping and is using the fact that silicon is transparent for wavelengths above ~1000nm. A void will therefor change the reflectance in that wavelength range. See datasheet below (Thanks to Jens Hemmingsen for the data). | It can also be used to map out voids after silicon wafer-bonding. This is done using the reflectance mapping and is using the fact that silicon is transparent for wavelengths above ~1000nm. A void will therefor change the reflectance in that wavelength range. See datasheet below (Thanks to Jens Hemmingsen for the data). | ||
Line 61: | Line 61: | ||
|style="background:LightGrey; color:black"|RPM viewer | |style="background:LightGrey; color:black"|RPM viewer | ||
|style="background:WhiteSmoke; color:black"| | |style="background:WhiteSmoke; color:black"| | ||
* | *Only on the local PC at the system | ||
|} | |} |
Latest revision as of 11:27, 3 February 2023
Feedback to this page: click here
PhotoLuminescence Mapper RPM2000
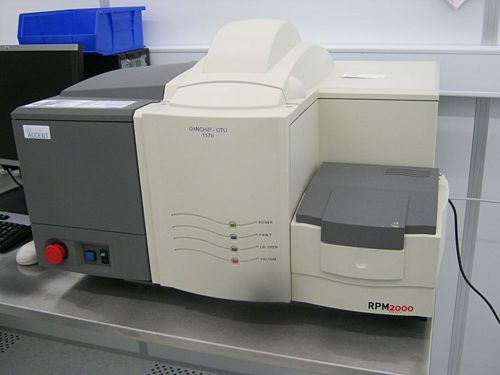
Unless otherwise stated, this page is written by DTU Nanolab internal
Photoluminescence mapping is a non-contact, non-destructive technique for mapping out uniformity of alloy composition, material quality and defects in substrates and of III-V epiwafers. The Rapid Photoluminiscence Mapper (RPM) is equipped with 3 lasers for PL measurements and a white-light source to map out thickness and reflectance of eg layers, microcavities and VCSELs.
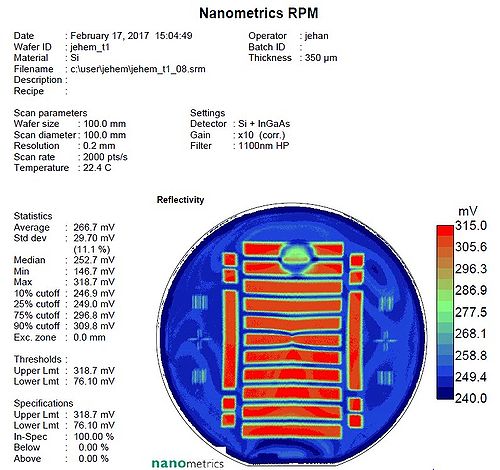
It can also be used to map out voids after silicon wafer-bonding. This is done using the reflectance mapping and is using the fact that silicon is transparent for wavelengths above ~1000nm. A void will therefor change the reflectance in that wavelength range. See datasheet below (Thanks to Jens Hemmingsen for the data).
The user manual and contact information can be found in LabManager:
Performance | Excitation |
|
---|---|---|
Detection |
| |
Gratings |
| |
Chuck sizes |
| |
Resolution |
| |
Wavelength accuracy |
| |
Materials | Allowed substrate materials |
|
Forbidden materials |
| |
Software | RPM viewer |
|