Specific Process Knowledge/Back-end processing/Polymer Injection Molder/SwitchOver: Difference between revisions
(10 intermediate revisions by 2 users not shown) | |||
Line 1: | Line 1: | ||
== Switch-over type == | == Switch-over type == | ||
The switch-over type is a very important setting. This setting defines when the injection-phase is done and thus when the machine will continue to the next phase of the injection molding cycle (after pressure / holding pressure). Since this setting defines when we consider injection is done it significantly | The switch-over type is a very important setting! It has a significant impact on the properties of the sample. This setting defines when the injection-phase is done and thus when the machine will continue to the next phase of the injection molding cycle (after pressure / holding pressure). Since this setting defines when we consider injection is done it significantly affects the properties of the produced sample, in particular filling. The switch-over settings are found on the 'Switchover type' screen (a sub-icon of the 'Inject' icon): | ||
[[File:03-switchover.png|600px|thumb|left|On the 'Switchover type' screen it's possible to select between volume, time, pressure, external and parallel switchover]] | [[File:03-switchover.png|600px|thumb|left|On the 'Switchover type' screen it's possible to select between volume, time, pressure, external and parallel switchover]] | ||
* | *'''Volume-dependent switchover''': A certain volume of polymer is injected. Note that the volume entered (3,2 cm<sup>3</sup> in this example) is not the volume injected, but the amount of polymer left after injection! Also note that changes in shot volume (the amount of polymer in the heating cylinder before injection) will also change injected volume unless the switch-over point is adjusted accordingly. Volume dependent switchover is particularly well suited for developing new injection molding processes (so you can gradually find the point where the cavity is almost filled and then work from there) or if you already know the exact volume of polymer required. | ||
* | *'''Time-dependent switchover''': After a certain amount of time, injection is considered complete. Not used very often because it offers very little control over both injection volume and pressure. | ||
* | *'''Injection pressure-dependent switchover''': Polymer is injected until a certain pressure is reached. Please note that the pressure in question is measured in the injection unit (heating cylinder). The pressure inside the cavity is not known. Special molds with an integrated pressure transducer is required to determine cavity pressures (very interesting, but unfortunately not available at DTU Nanolab). This switchover type is very easy to use and is not influenced by e.g. changes in shot volume. The selected switchover pressure (in this example 800 bar) is critical for replication. Very low switchover pressures can result in bad replication or even incomplete filling while too high pressure can cause the sample to stick so well to the shim, that it gets very difficult to demold. | ||
*'''External switchover''': Injection continues until a signal is received from an external device (e.g. an external pressure transducer). Can not be used, since no external devices are currently available. | |||
*'''Parallel switchover''': Injection is defined by a combination of parameters. Has never been used until now. |
Latest revision as of 14:57, 6 August 2020
Switch-over type
The switch-over type is a very important setting! It has a significant impact on the properties of the sample. This setting defines when the injection-phase is done and thus when the machine will continue to the next phase of the injection molding cycle (after pressure / holding pressure). Since this setting defines when we consider injection is done it significantly affects the properties of the produced sample, in particular filling. The switch-over settings are found on the 'Switchover type' screen (a sub-icon of the 'Inject' icon):
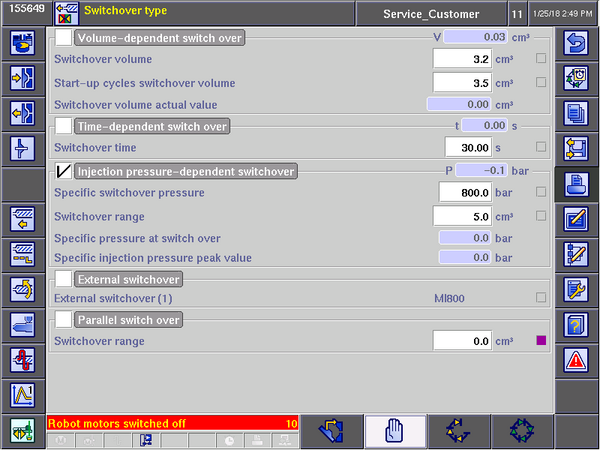
- Volume-dependent switchover: A certain volume of polymer is injected. Note that the volume entered (3,2 cm3 in this example) is not the volume injected, but the amount of polymer left after injection! Also note that changes in shot volume (the amount of polymer in the heating cylinder before injection) will also change injected volume unless the switch-over point is adjusted accordingly. Volume dependent switchover is particularly well suited for developing new injection molding processes (so you can gradually find the point where the cavity is almost filled and then work from there) or if you already know the exact volume of polymer required.
- Time-dependent switchover: After a certain amount of time, injection is considered complete. Not used very often because it offers very little control over both injection volume and pressure.
- Injection pressure-dependent switchover: Polymer is injected until a certain pressure is reached. Please note that the pressure in question is measured in the injection unit (heating cylinder). The pressure inside the cavity is not known. Special molds with an integrated pressure transducer is required to determine cavity pressures (very interesting, but unfortunately not available at DTU Nanolab). This switchover type is very easy to use and is not influenced by e.g. changes in shot volume. The selected switchover pressure (in this example 800 bar) is critical for replication. Very low switchover pressures can result in bad replication or even incomplete filling while too high pressure can cause the sample to stick so well to the shim, that it gets very difficult to demold.
- External switchover: Injection continues until a signal is received from an external device (e.g. an external pressure transducer). Can not be used, since no external devices are currently available.
- Parallel switchover: Injection is defined by a combination of parameters. Has never been used until now.