Specific Process Knowledge/Back-end processing/Polymer Injection Molder/Nozzle: Difference between revisions
(9 intermediate revisions by 2 users not shown) | |||
Line 1: | Line 1: | ||
== Nozzle/tower settings == | == Nozzle/tower settings == | ||
On the ''''Nozzle'''' screen it is possible to adjust settings for how the nozzle moves back and forth during the injection molding cycle and how it presses against the inlet port of the tool: | |||
[[File:12-nozzlemove.png|600px|thumb|left|Movement of the tower (nozzle) is controlled on the 'Tower' screen.]] | [[File:12-nozzlemove.png|600px|thumb|left|Movement of the tower (nozzle) is controlled on the 'Tower' screen.]] | ||
Line 9: | Line 9: | ||
*'''Retract profile''': This parameter controls the speed profile as the tower moves backwards and retracts the nozzle from the mold inlet port. Again, the default settings will work fine for most applications. | *'''Retract profile''': This parameter controls the speed profile as the tower moves backwards and retracts the nozzle from the mold inlet port. Again, the default settings will work fine for most applications. | ||
<br> | <br> | ||
*'''Nozzle stroke''': This setting controls how far the nozzle moves back between shots. Usually a value between 40 - 100 mm will work fine. | *'''Nozzle stroke''': This setting controls how far the nozzle moves back between shots. Usually a value between 40 - 100 mm will work fine. If you experience problems with long fine (thin) threads of polymer from the sprue of your samples, it may help to increase the nozzle stroke a little. This will move the nozzle tip further away from the inlet port between injections and thus reduce heat-up of the inlet port. The temperature of the inlet port will also influence polymer flow during injection. | ||
<br><br><br><br><br><br><br><br> | <br><br><br><br><br><br><br><br><br><br><br><br><br> | ||
Scrolling down will reveal a few more important settings regarding nozzle control: | Scrolling down will reveal a few more important settings regarding nozzle control: | ||
<br> | |||
[[File:09-tower.png|600px|thumb|left|Scrolling down on the 'Tower' screen reveals additional nozzle settings.]] | [[File:09-tower.png|600px|thumb|left|Scrolling down on the 'Tower' screen reveals additional nozzle settings.]] | ||
<br><br><br><br> | <br><br><br><br><br> | ||
*''' | *'''Force build-up time''': This setting defines how long time the machine has to build up the nozzle contact force. A value of 0,2-0,5 sec works fine for most applications | ||
<br> | <br> | ||
*''' | *'''Contact force''': This parameter defines how hard the nozzle presses against the inlet port during injection and after/holding pressure. '''Please do not increase this value above 15 kN without contacting DTU Nanolab as this may damage the nozzle tip or the mold inlet port!''' For polymers that undergo significant shear thinning (such as PP and PE) contact forces around 14 kN can be required (depends on injection speed) while lower contact forces (10 - 12 kN) will be sufficient for most other polymers. | ||
<br> | <br> | ||
*''' | *'''Delay time retraction''': In some cases it may be desirable to maintain the inlet port at high temperature after injection and holding/after pressure. In this case a delay can be entered here (usually 5 - 10 seconds is fine). Keep in mind that if the sum of 'Plasticizing delay time' described earlier and the 'Delay time retraction' on this page exceeds the cooling time, this will cause a delay in the injection molding cycle (thus increasing the effective cooling time). |
Latest revision as of 15:22, 16 January 2020
Nozzle/tower settings
On the 'Nozzle' screen it is possible to adjust settings for how the nozzle moves back and forth during the injection molding cycle and how it presses against the inlet port of the tool:
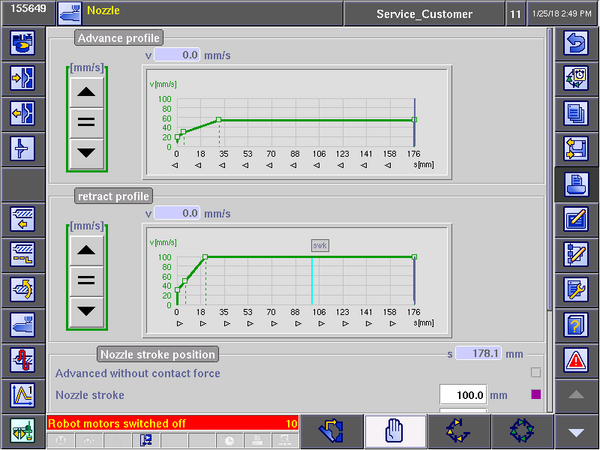
- Advance profile: This parameter controls the speed profile as the tower moves forward to press the nozzle against the mold inlet port. The default settings work fine for most applications.
- Retract profile: This parameter controls the speed profile as the tower moves backwards and retracts the nozzle from the mold inlet port. Again, the default settings will work fine for most applications.
- Nozzle stroke: This setting controls how far the nozzle moves back between shots. Usually a value between 40 - 100 mm will work fine. If you experience problems with long fine (thin) threads of polymer from the sprue of your samples, it may help to increase the nozzle stroke a little. This will move the nozzle tip further away from the inlet port between injections and thus reduce heat-up of the inlet port. The temperature of the inlet port will also influence polymer flow during injection.
Scrolling down will reveal a few more important settings regarding nozzle control:
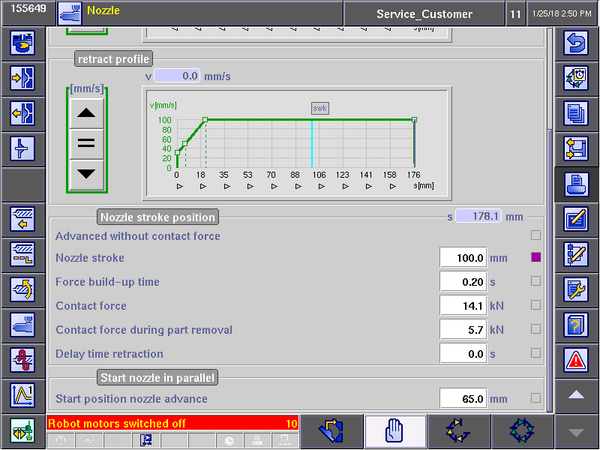
- Force build-up time: This setting defines how long time the machine has to build up the nozzle contact force. A value of 0,2-0,5 sec works fine for most applications
- Contact force: This parameter defines how hard the nozzle presses against the inlet port during injection and after/holding pressure. Please do not increase this value above 15 kN without contacting DTU Nanolab as this may damage the nozzle tip or the mold inlet port! For polymers that undergo significant shear thinning (such as PP and PE) contact forces around 14 kN can be required (depends on injection speed) while lower contact forces (10 - 12 kN) will be sufficient for most other polymers.
- Delay time retraction: In some cases it may be desirable to maintain the inlet port at high temperature after injection and holding/after pressure. In this case a delay can be entered here (usually 5 - 10 seconds is fine). Keep in mind that if the sum of 'Plasticizing delay time' described earlier and the 'Delay time retraction' on this page exceeds the cooling time, this will cause a delay in the injection molding cycle (thus increasing the effective cooling time).