Specific Process Knowledge/Thin film deposition/Deposition of Nickel/Electroplating of nickel: Difference between revisions
No edit summary |
|||
Line 7: | Line 7: | ||
== DTU Danchip Standard Programs == | == DTU Danchip Standard Programs == | ||
Four different Danchip standard programs have been made. They have all been made to fabricate nickel shims for use in the polymer injection molder at Danchip. For this purpose a nickel thickness of around | Four different Danchip standard programs have been made. They have all been made to fabricate nickel shims for use in the polymer injection molder at Danchip. For this purpose a nickel thickness of around 330-340 µm is required. By experimentation it has been found that the required charge for this sample thickness is 18,0 Ah. The only difference between the four different standard programs are the time required for depositing the nickel. The four different standard programs deposit 330-340 µm of nickel in about 3, 4, 6 and 12 hours respectively. | ||
The following figure shows the current profile during the first 2 hours of the programs: | The following figure shows the current profile during the first 2 hours of the programs: |
Revision as of 15:15, 24 September 2013
Electroplating of nickel: Danchip standard processes
Feedback to this page: click here
DTU Danchip Standard Programs
Four different Danchip standard programs have been made. They have all been made to fabricate nickel shims for use in the polymer injection molder at Danchip. For this purpose a nickel thickness of around 330-340 µm is required. By experimentation it has been found that the required charge for this sample thickness is 18,0 Ah. The only difference between the four different standard programs are the time required for depositing the nickel. The four different standard programs deposit 330-340 µm of nickel in about 3, 4, 6 and 12 hours respectively.
The following figure shows the current profile during the first 2 hours of the programs:
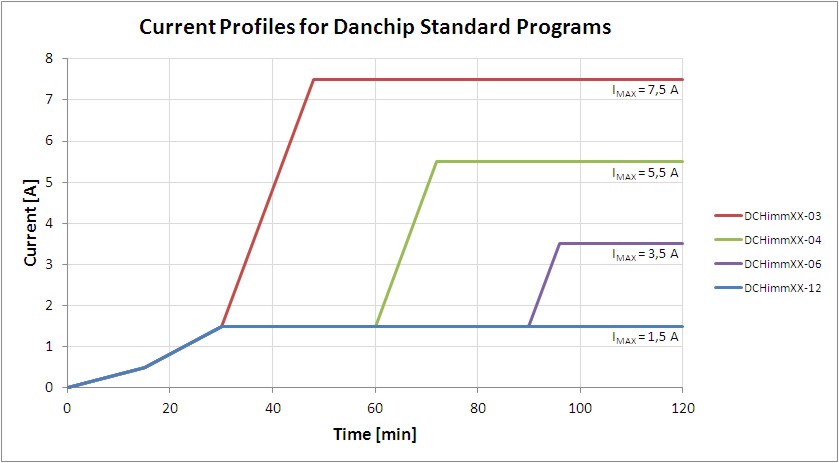
As can be seen from the illustration the first 30 minutes of all standard processes are identical. All processes use a slow ramping of the current. This is to make sure that some material is deposited which can conduct a higher current. Starting a plating process at several amperes is very likely to damage the sample (and possibly the sample holder) because the seed layer (usually 75-120 nm thick) cannot support that high currents.
The Standard programs are named using the following convention: DCHimmXX-YY where DCH indicates it's a process developed by Danchip, imm that is a process developed for producing samples for the injection molding machine, XX denotes the charge in Ah (Ampere-hours) and YY denotes the approximate process time in hours.
Comparison of standard processes
DCHimm18-03 | DCHimm18-04 | DCHimm18-06 | DCHimm18-12 | |
---|---|---|---|---|
Charge [Ah] | 18 | 18 | 18 | 18 |
Expected nickel thickness | 320-330 µm | 320-330 µm | 320-330 µm | 320-330 µm |
Maximum current [A] |
7,5 |
5,5 |
3,5 |
1,5 |
Process time [hh:mm:ss] |
02:41:01 |
xx:xx:xx |
xx:xx:xx |
12:16:01 |
Process comments |
Fastest possible process (maximum allowable current). One must accept the following (often unwanted) material properties: high stress levels in deposited nickel, high roughness, quite ductile nickel. |
A fast program that allows one to produce two samples in a normal working day. Similar material properties as stated for the 3 hour process, although slightly less 'severe'. |
A compromise between desired material properties (hardness, ductility, roughness) and process time. Will result in a sample that will be useful for most standard injection molding processes. |
A slower process that in return results in lower roughness and stronger mechanical properties. A good choice for shims that will be used with 'harsh' injection molding parameters (high temperatures and high pressures). |