Specific Process Knowledge/Lithography/Coaters: Difference between revisions
Line 105: | Line 105: | ||
|style="background:WhiteSmoke; color:black"| | |style="background:WhiteSmoke; color:black"| | ||
* No permanent media | * No permanent media | ||
|colspan=" | |colspan="2" rowspan="2" align="center" style="background:WhiteSmoke; color:black"|Only manual dispense | ||
|colspan="1" rowspan="2" align="center" style="background:WhiteSmoke; color:black"|Only manual dispense | |||
|style="background:WhiteSmoke; color:black"| | |style="background:WhiteSmoke; color:black"| | ||
* No permanent media | * No permanent media |
Revision as of 12:26, 24 March 2017
Coater Comparison Table
Equipment | Spin Coater: Gamma UV | Spin Track 1 + 2 | SSE Spinner DECOMMISSIONED! | Spin Coater: RCD8 | Spin Coater: Manual All Resist | Spin Coater: Manual Standard Resists | Spin Coater: Manual All Purpose | Spray Coater | |
---|---|---|---|---|---|---|---|---|---|
Purpose |
|
|
|
|
|
|
|
| |
Performance | Substrate handling |
|
|
|
|
|
|
| |
Permanent media |
|
|
|
|
Only manual dispense | Only manual dispense |
| ||
Manual dispense option |
|
|
|
|
| ||||
Process parameter range | Spindle speed |
|
|
|
|
|
|
|
|
Gyrset |
|
|
|
|
|
|
|
||
Substrates | Substrate size |
|
|
|
|
|
|
|
|
Batch size |
|
|
|
|
|
|
|
| |
Allowed materials |
|
|
|
|
|
|
|
|
Spin coating
The process of spin coating consists of a selection of the following steps:
- Priming (typically HMDS)
- Acceleration to a low spin speed if dynamic dispense is used
- Resist dispense (static or dynamic)
- Resist spreading at low spin speed
- Spin-off
- Backside rinse (typically during spin-off)
- Edge-bead removal
- Softbake (contact or proximity)
After priming, the wafer is centered on the coater chuck and held in place by vacuum, or in some cases pins. If static dispense is used, the wafer remains static during the ensuing resist dispense. In the case of dynamic dispense, the wafer rotates at low spin speed during the dispense. Using too high spin speed during dispense can cause surface wetting issues, while a too low spin speed causes the resist to flow onto the backside of the wafer. After dispense, a short spin at low spin speed may be used in order to spread the resist over the wafer surface before spin-off.
Spin-off
The spin-off cycle determines the thickness of the resist coating. For a given resist, the thickness is primarily a function of the spin-off speed and the spin-off time, both following an inverse power-law (y=k*x^-a). The acceleration to the spin-off speed also influences the thickness, but the effect is dependent on previous steps. The spin-off is usually a simple spin at one speed, but it may be comprised of several steps at different spin speeds. After spin-off, the wafer is decelerated.
The coated thickness, t, as a function of the spin-off speed, w, follows an inverse power-law, t = k * w-a. The constant, k, is a function of the resist viscosity and solid content, and the spin-off time. The exponent, a, is dependent on solvent evaporation, and is typically ~½ for UV resists. This means that from the thickness t1 achieved at spin speed w1, one can estimate the spin speed w2 needed to achieve thickness t2 using the relation:
t1*w1½ = t2*w2½ => w2 = w1 * t12/t22.
For thick SU-8, however, a is observed to be ~1 (probably due to the low solvent content and/or the formation of skin). In this case, the relation simply becomes:
t1*w1 = t2*w2 => w2 = w1 * t1/t2.
Backside rinse
Dependent on the spin speeds used in the various steps of the spin coating, resist may creep over the edge of the wafer and onto the backside. Also, some resists tend to leave fine strings of resist protruding from the edge of the wafer, or folded onto the backside, an effect sometimes referred to as "cotton candy". This resist will contaminate the softbake hotplate, and thus subsequent wafers with resist. In a backside rinse step, solvent administered through a nozzle to the backside of the wafer while spinning at low or medium spin speed dissolves the resist and washes it away. After the rinse, a short spin at medium spin speed dries the wafer before the softbake. During the backside rinse solvent inevitably creeps onto the front side of the wafer. This effect may be used to dissolve and subsequently remove an edge-bead, but it may also leave the rim of the wafer exposed. As an alternative to backside rinse, a wafer which is left dirty on the backside by the spin coat process may be softbaked in proximity in order to protect the hotplate from contamination. This leaves front side coating intact, but also leaves the backside dirty.
Edge bead
During spin coating, resist builds up at the edge of the wafer due to the change in surface tension at the edge. This phenomenon is called an edge-bead. Dependent on spin coating parameters, the coating may be several times thicker at the edge than in the central area. In a subsequent hard contact exposure step, this edge-bead induces an undesired proximity gap which reduces the lateral resolution, and may even cause the wafer to stick to the mask.
In an edge-bead removal step, solvent administered through a nozzle positioned at the edge of the wafer while spinning at low or medium spin speed dissolves the resist and washes it away. After the removal, a short spin at medium spin speed dries the wafer before the softbake. Dependent on the viscosity (solvent content) of the resist at the point of edge-bead removal, this drying spin may cause the resist to re-flow and create a secondary edge-bead. In some cases, it may be necessary to (partially) softbake the resist before edge-bead removal.
Softbake
After spin coating, the solvent in the resist formulation must be evaporated in a baking step in order to solidify the resist. This softbake can be carried out as a contact bake or a proximity bake. In a contact bake, the wafer is held in close contact to the hotplate surface while resting on shallow bumps only 150µm above the hotplate. In a proximity bake, the wafer is first moved into proximity, e.g. 1mm, of the hotplate surface, then held there (on the lift pins) for the duration of the bake.
Spin coaters at Danchip
Spin Track 1 + 2

Feedback to this section: click here
Spin Track 1 + 2 is an SVG 88 series track system from Rite Track. Each track consists of a HMDS priming module, a spin coating module, and a baking module. In fact, the only difference between the two tracks is the resist used in the spin coating module. Spin Track 1 + 2 is capable of handling 150 mm wafers, as well as 100 mm wafers, but is currently set up for 100 mm wafer processing.
The Spin Track 1 + 2 is controlled using the Recipe Manager software via the touchscreen on the arm attached to the lefthand end of the track. Recipes for the individual modules are developed by Danchip and combined into flows. The user selects a flow (specific to track 1 or 2), and the appropriate recipes will be downloaded and executed on the appropriate track. The other track runs an empty process (no wafers needed), and can unfortunately not be used by a second user while the first user is processing.
The user manual, user APV, and contact information can be found in LabManager
Process information
- General Spin Track 1 + 2 process information
- HMDS priming on Spin Track 1 and 2
- AZ MiR 701 (29cps) coating on Spin Track 1
- AZ nLOF 2020 coating on Spin Track 2
- Post-exposure baking on Spin Track 2
Spin Track | 1 | 2 | |
---|---|---|---|
Purpose |
|
| |
Resist |
AZ MiR 701 (29cps) positive tone |
AZ nLOF 2020 negative tone | |
Performance | Coating thickness |
1 - 3 µm |
1 - 4 µm |
HMDS contact angle |
60° - 90°; standard recipe 82° (on SiO2) | ||
Process parameters | Spin speed |
10 - 9990 rpm | |
Spin acceleration |
1000 - 50000 rpm/s | ||
Hotplate temperature |
90°C |
110°C | |
HMDS priming temperature |
50°C | ||
Substrates | Substrate size |
100 mm wafers | |
Allowed materials |
Silicon and glass wafers Film or pattern of all types | ||
Batch |
1 - 25 |
Spin Coater: Gamma UV
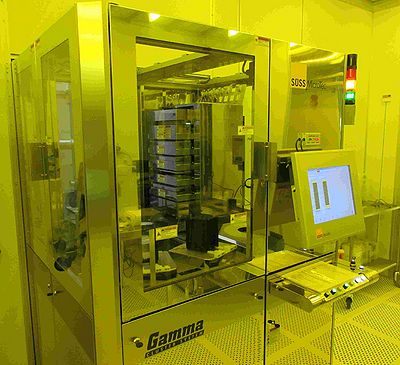
Feedback to this section: click here
Spin Coater: Gamma UV was installed at Danchip in March 2015. It is a Gamma 2M cluster from Süss MicroTec with spin coating, vapour priming, and baking modules. The system handles 4" and 6" wafers without size conversion, and can be set up to handle 2" or 8".
The coater is equipped with 3 different resists lines:
- AZ MiR 701
- AZ nLOF 2020
- AZ 5214E
and
- 1 syringe, which can be used for various resists.
The processes that are available on the system are developed by Danchip. Upon request, it is possible to establish new processes. Use of the syringe requires special training, and would as a starting point require batches in excess of 20 wafers.
The user manual, user APV, and contact information can be found in LabManager
Process information
Purpose |
| |
---|---|---|
Resist |
| |
Performance | HMDS contact angle |
60 - 80° |
Coating thickness |
| |
Process parameters | Priming temperature |
120 °C |
Spin speed |
10 - 6000 rpm | |
Spin acceleration |
10 - 10000 rpm/s | |
Hotplate temperature |
25 - 200 °C | |
Cool plate temperature |
21 °C | |
Substrates | Substrate size |
|
Allowed materials |
Silicon and glass | |
Batch |
1 - 25 |
1) Requires tool change.
Spin Coater: Gamma E-beam and UV 
Feedback to this section: click here
Spin Coater: Gamma E-beam and UV will be installed at Danchip in June 2017. It is a Gamma 4M cluster from Süss MicroTec with spin coating, vapour priming, and baking modules. The system handles 2", 4", and 6" wafers without size conversion, using two separate coater stations.
The 2" coater station is equipped with 2 different resists lines:
- AR-P 6200.09 (CSAR)
- AZ 5214E
and
- 1 syringe, which can be used for various resists.
The 4"/6" coater station is equipped with 4 different resists lines:
- AR-P 6200.09 (CSAR)
- AZ 5214E
- AZ 4562
- AZ MiR 701
The processes that are available on the system are developed by Danchip. Upon request, it is possible to establish new processes. Use of the syringe requires special training, and would as a starting point require batches in excess of 20 wafers.
Purpose |
| |
---|---|---|
Resist |
| |
Performance | HMDS contact angle |
60 - 80° (on Silicon) |
Coating thickness |
| |
Process parameters | Priming temperature |
120 °C |
Spin speed |
10 - 6000 rpm | |
Spin acceleration |
10 - 10000 rpm/s | |
Hotplate temperature |
25 - 200 °C | |
Cool plate temperature |
21 °C | |
Substrates | Substrate size |
|
Allowed materials |
Silicon and glass | |
Batch |
1 - 25 |
Spin Coater: RCD8
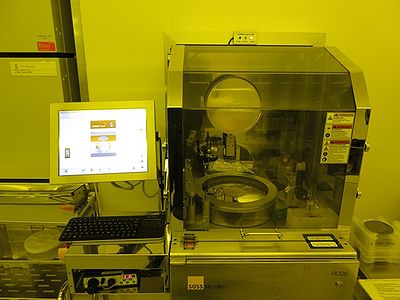
Feedback to this section: click here
Spin Coater: RCD8 is a model RCD8 T spin coater from Süss MicroTec with a motorized media arm and Gyrset functionality. It's primary purpose is spin coating of SU-8 resist. However, due to the possibility of using a non-vacuum chuck, the spin coater is also suitable for coating of substrates with e.g. textured backsides or membranes.
The user manual, user APV, and contact information can be found in LabManager
Process information
Purpose |
| |
---|---|---|
Resist |
| |
Performance | Coating thickness |
|
Process parameters | Spin speed |
Vacuum chuck: 10 - 5000 rpm |
Spin acceleration |
10 - 3000 rpm/s | |
Substrates | Substrate size |
|
Allowed materials |
All cleanroom materials ? | |
Batch |
1 |
Manual Spin Coaters
Go back to Coater comparison table.
![]() |
![]() |
|
Spin Coater: Manual All Resist | Spin Coater: Manual Standard Resists | Spin Coater: Manual All Purpose |
Loacted in fumehood in A-5 | Located in fumehood in E-5 | Located in fumehood in C-1 |
LabSpin 6, Süss MicroTec | LabSpin 6, Süss MicroTec | WS-650, Laurell |
LabManager | LabManager | LabManager |
Training video: LabSpin6
Spin curves (LabSpin 6): AZ 5214E, AZ nLOF 2020, ZEP 520A, FOX-15, AZ 4562, CSAR 6200