Specific Process Knowledge/Thermal Process/A4 Phosphor Pre-dep furnace: Difference between revisions
Line 49: | Line 49: | ||
|style="background:WhiteSmoke; color:black"| | |style="background:WhiteSmoke; color:black"| | ||
*Silicon wafers (new from the box or RCA cleaned) | *Silicon wafers (new from the box or RCA cleaned) | ||
*In doubt: look at the cross contamination | *In doubt: look at the [http://www.labmanager.danchip.dtu.dk/view_binary.php?fileId=1250 cross contamination chart] or please send a mail to [mailto:furnace@danchip.dtu.dk furnace@danchip.dtu.dk] | ||
|- | |- | ||
|} | |} |
Revision as of 14:06, 26 November 2012
A4 Furnace Phosphor pre-dep
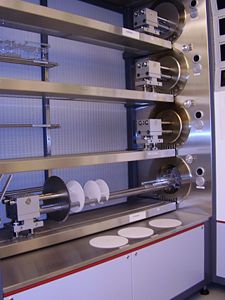
A4 is a furnace to dope Si wafers with Phosphor to make conductive lanes, etch stops etc. The doping source is Phosphoryl chloride (commonly called phosphorus oxychloride) is a colourless liquid with the formula POCl3.
A4 is the lowest furnace tube in the A-stack positioned in cleanroom 2. The A-stack together with furnace C2 are the cleanest of all our furnaces. Please be aware of which substrates are allowed to enter this furnace. Check the cross contamination chart. If you are in doubt, please send a mail to furnace@danchip.dtu.dk.
The user manual(s), quality control procedure(s) and results, user APV(s), technical information and contact information can be found in LabManager:
Process knowledge
Purpose | Doping of Phosphor | |
---|---|---|
Performance |
| |
Process parameter range | Process Temperature |
|
Process pressure |
| |
Gasses on the system |
| |
Substrates | Batch size |
|
Substrate material allowed |
|